with šļø Antoine WALTER ā Podcaster in Chief @ GF Piping Systems
š§ GF Piping Systems is the global expert for the safe and reliable transportation of water, chemicals, and gas.
This episode is part of my series on Water Digitization ā check it out! š
Table of contents
What we covered:
ā”ļø We just turned 2ā000 downloads with theĀ #podcast, and I still canāt believe it!
I remember that anecdote when I was three weeks into the experiment.Ā
I was discussing with one of these āinfluencer gurusā.Ā
She asked, āso whatās your show about?ā
āWater & Wastewater Treatmentā
āWell, that sounds nicheā¦ā š
I smiled and went on.
7.8 billion people rely on water to survive. If thatās a niche, I donāt know whatās not! š¤
Fast forward to last week: we not only passed the 2ā000 downloads but also reached 75ā000 infographic views on LinkedIn!
I get this is still baby steps compared to beauty influencers on Instagram.
But itās something, and Iām so glad we achieved this something!
Every step towards better information sharing in theĀ #waterindustryĀ counts!Ā
Every step towards the preservation of water counts. š¤
So to celebrate together, and summarize one of the main trends my guests have been addressing over the last weeks, I prepared you a special episode:
ā How to cleverly embrace the digital crazeā
The š„ rapid-fire questionsš„ Ā are this time for you:
ā”ļø What topics would you like us to address in the coming weeks?
ā”ļø What is the trend we shall explore?
ā”ļø Who should I invite?
Iām thrilled to read your answers!Ā
ā”ļø Get the 5 Page Synthesis for free!
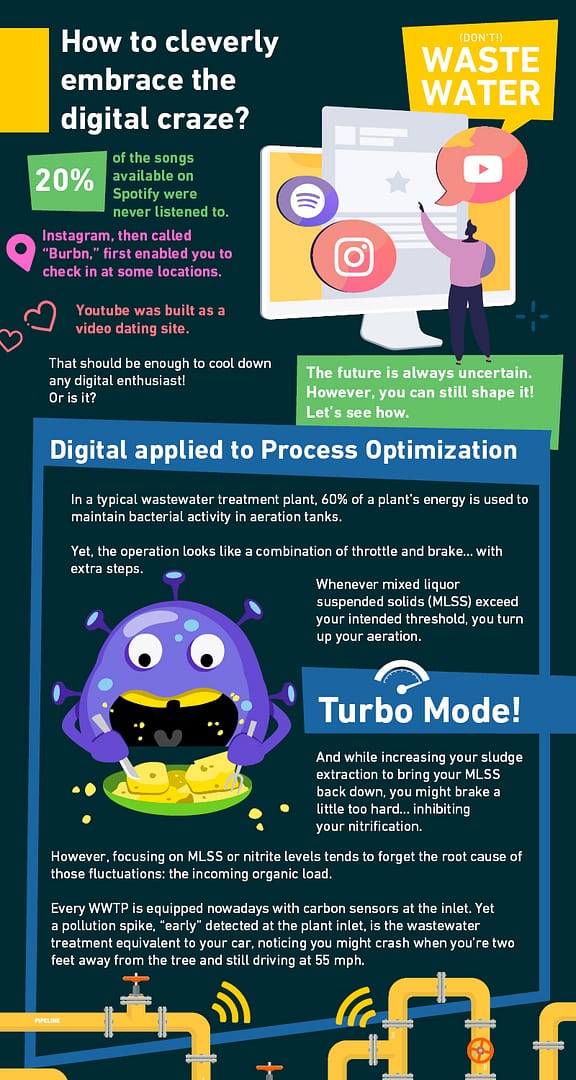
Resources:
ā”ļø Send your warm regards to our beloved Sponsor on their website!
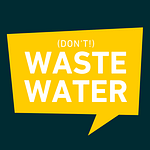
is on Linkedin ā”ļø
Full transcript:
20% of the songs available on Spotify were never listened to. Not so long ago, Instagram (then called āBurbnā) enabled you to check in at some locations, earn points to hang out with friendsĀ and ā as an afterthought ā to take pictures. Oh, and YouTube was built to be a video dating site.
Well there you are! Fully equipped to cool down a digital enthusiast, the next time he proclaims that IOT is the future of water and wastewater treatment. But wait, should you?
In fact, the stories these anecdotes tell are a bit different.
Why would you upload thousands of songs and keep them on your data centers if no one ever calls them? Simply because, you had no way at first to determine which ones would be endlessly listened to.
Sure, an early-adopter of Burbn, checking in at Mount Rushmore while waiting for his YouTube date might hardly recognize what both platforms have become. Yet, his behavior at the time framed those digital behemoths, gaining them billions of subscribers (and dollars) on the way.
Future is always uncertain. However, you can still shape it.
Digital applied to Process Optimization
As water professionals, we know that our processes always have room for improvement ā and thatās an understatement.
Take a typical wastewater treatment plant. Aeration tanks burn about 60% of a plantās energy, essentially to maintain bacterial activity. It is yet very common to use a combination of throttle and break to keep those microscopic workers in their comfort zone.
You know the story: whenever the mixed liquor suspended solids (MLSS) exceed your intended threshold, you turn up your aeration (the infamous and energy gluttonous āturbo modeā). Then, while increasing your sludge extraction to bring your MLSS back down, you might brake a little too hard⦠and end-up inhibiting your nitrification.
Factor in that whenever you change your sludge extraction ratio that affects other areas of the plant (settling tanks, digestersā¦) and even if still on helicopter view, you get a sense of operation complexity.
However, focusing on MLSS or nitrite levels tends to forget the root cause of those fluctuations: the incoming organic load.
Every WWTP is equipped nowadays with carbon sensors at the inlet. Yet a pollution spike, āearlyā detected at the plant inlet, is the wastewater treatment equivalent to your car detecting you might crash, when youāre two foot away from the tree and still driving at 55 mph.
Your plant is not lying in the middle of a desert, treating wastewater it creates. It is instead connected to a sewer, where residence times range from hours to days.
Sow today to reap tomorrow
The spike in organic load which causes your headache when reaching the plant probably appeared some hours ago somewhere in the sewage network.
Imagine if neither you, nor the original polluter were to accept the passive status quo! Pollution could be reduced at source, while you would prepare your microbial chaps to hold the siege.
Nevertheless, collecting organic load data on sewage networks is not easy as pie. First, the corrosive atmosphere in the sewer doesnāt really make it a go-to place for a happy gathering. Second, complex sensors did not become instantly cheaper just to support your optimization crusade.
This is where data has your back.
It is absolutely doable to build models that use simple indicators (pH, conductivity, temperatureā¦) to extrapolate quality factors (like organic load). It ājustā requires you to build a critical mass on data.
This is neither science fiction, nor rocket science as Ari Goldfarb explained in Episode 6 of the ā(donāt) Waste Waterā podcast. Companies of the likes of Kando or Emagine simply leverage AI and Machine Learning on one end, of-the-shelf sensors on the other to provide helpful insights on sewer and pollution loads.
Operators that used to detect one quality shift per month while wondering why they had to heavily play with the turbo mode, now notice that quality actually shifts 3-4 times per week.
Meanwhile, industrials that had no clue so far they were a pollution source received a welcome revelation that might prevent them from repeating some mistakes in the future.
Hereās a first take-home message: start gathering data today, even if you donāt yet exactly know what for. Donāt go for the fancy: keep it simple and consistent. The models you might feed with it one day thank you in advance ā so does your stunt double with grey hair that will have to pay the energy bills by then.
As much as you might agree at this stage with the Idea that there is room for optimization in each plant, I could swear you still wonder how big of a potential this represents. So did I not so long ago.
Revealing the untapped potential of existing plants
While recording Episode 3 of my podcast series, Thomas Debruyne shared some numbers on plants that underwent the digital diagnosis and remedy route Veolia Water Technologies markets under their Aquavista brand.
Two of those might simply blow your mind. A WWTP in Denmark reduced its operating costs by 40% while increasing its hydraulic capacity by 80%!
Just think of it that way: thereās no need to expand a plant if you can reach thus large untapped capacity. Said differently, this last number implies a tremendous saving on investment.
Too good to be true? Jeroen de Lathouver from Waterleau shared similar experience when interviewing on Hakim El Fadilās āSmart Water Solutionsā podcast. So did Jonathan Grant from Emagin on Dave McGimpseyās.
When you hear the same lines from various non-connected individuals and companies, chances are there is truth lying beneath (and if not yet done, you probably should start listening to podcasts).
A 3-step process
To reap the process optimization benefits, just apply this simple recipe.
First, make sure to collect the right data at the right place. Second, use this entry to run a diagnosis of the plant, and build up a model (aka Digital Twin) that computes the process behavior. Third, run process and control hypotheses on the digital twin to find out which ones deliver the best output, and share those insights with the plant operators.
It is then up to you to launch such an initiative on your own or to get the support of companies of the likes of the ones mentioned before.
WWTPs are actually not the only playground for this methodology. Applying it upstream, within the factories that contribute to the pollution events, might also rank as a value move.
Digital can also support factories
Industrial operators donāt pollute for the sake of harming the environment while smoking cigars and drinking Brandy. It has much more to do with a lack of understanding of the water cycle within their plant.
As embedded and necessary to their processes as water might be, the core of a factoryās mission still lies in the production of an industrial good. Which means that plant operators have little focus on the water cycle, when they notice at all there is one.
However, acquiring data on process and wastewater streams and using it to run a diagnosis often acts as an eye-opener. As Stephane Gilbert, CEO of Aquassay reported in Episode 5, this exercise allowed to divide downtime on a factoryās reverse osmosis skids by 15⦠at the only expense of an additional valve.
If water is not everywhere on the radar, operation costs surely are. Factoring in the opportunity of a data driven preventive maintenance should achieve to convince industrial players: it almost builds for a no-downtime guarantee.
For sure, digital is not going to disrupt and replace your plant operators. But it will lighten the load on their shoulders upon making a decision while giving them headspace to take action on all the other tasks a human still accomplishes better than any machine.
Statistics say, youāre watching your smartphone 150 times per day and reacting on an SMS within 4 minutes. Why would you still rely on a single daily analysis and your operatorās gut feeling to run complex water processes? Act on the incongruity today: youāre also allowed to reap the benefits of the digital craze!
2 thoughts on “How to Cleverly Embrace the Digital Craze in the Water Industry?”