There’s a company that can boast having worked on turning any possible source of Lithium to battery grade: Veolia. How does the Water Giant double down as a lithium refinery builder? Let’s find out.
Find out more with my entire Lithium deep dive.
with 🎙️ Jim Rieke – VP of Process Engineering at Veolia Water Technologies
💧 Veolia Water Technologies specializes in water treatment solutions while providing a complete range of services for industrial & public authorities
Lithium Refinery – Slider
Slider-Jim-Rieke-Veolia-Water-Technologies-Lithium-Refinery-turning-Lithium-Carbonate-to-Battery-Grade-Lithium-HydroxideWhat we covered:
👷 How HPD onboards all its hires through its service and commissioning groups and how that’s the best learning experience to Veolia Water Technologies’ portfolio
🤝 How the milestone Naraha Lithium Refinery reference started through a collaboration between Orocobre (now, Allkem) and HPD and what was the step by step road to success
🚢 What’s the magic that turns Lithium Carbonate in South America into Lithium Hydroxide Monohydrate in Japan
🧩 How there might be standard building blocks but how every lithium carbonate is slightly different and hence requires a tailor-made lithium refining process
🏭 Where do impurities appear in a lithium refinery process and how to remove them to guarantee a battery-grade output
🧰 How extracting lithium from clay is still a very new process and what it changes in the lithium refinery set up
🛠️ How Veolia Water Technologies’ holistic approach is a key differentiator in the development of a lithium refinery
🌍 How geopolitics and government incentives play a role in the economics of a lithium refinery
👰 How the newly wed SUEZ and Veolia offer an even broader portfolio of complimentary technologies to better serve the lithium market
📈 How DLE “suddenly” makes much more lithium available and how HPD’s lithium refinery process copes with the source’s specificities
♻️ How batter-grade lithium is just one of the outputs of a lithium refinery: Veolia Water Technologies’ expertise also allows to valorize several more by-products along the way
💰 How Veolia Water Technologies’ involvement in projects can help get junior lithium companies get financed as a valuable reference partner
🗺️ Building a Lithium Refinery step by step; leaching, evaporation, crystallization, ion exchange: the lithium refinery keywords; lithium refining in the broader scheme of the EV battery vertical; turning sodium sulfate into sodium hydroxide and sulfuric acid; empowering circularity… and much more!
🔥 … and of course, we concluded with the 𝙧𝙖𝙥𝙞𝙙 𝙛𝙞𝙧𝙚 𝙦𝙪𝙚𝙨𝙩𝙞𝙤𝙣𝙨 🔥
Resources:
🔗 Come say hi to Jim on Linkedin
🔗 Check Standard Lithium’s website
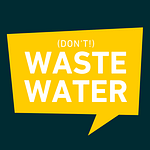
is on Linkedin ➡️
Teaser
Table of contents
Full Transcript:
These are computer-generated, so expect some typos 🙂
Antoine Walter: Hi Jim. Welcome to the show.
Jim Rieke: Hey Antoine, great to be here.
Antoine Walter: I’m looking forward that conversation for many reasons. The first being that, you know, Veolia is the big dog in the water industry, and I had a couple of interviews with Veolia guys, but not as much as statistically I should have within the amount of podcasts already published. So you’re here to repair that mistake.
And much more importantly, we are digging into a topic, which sounds really fascinating. I guess it’s gonna be really about lithium refining, but also everything which is around that. But before going into the deep dive, let’s start with the tradition on that microphone, which is to open with a postcard.
What can you tell me about Plainfield, Illinois, which I would ignore by now.
Jim Rieke: Plainfield, Illinois, it’s a suburb of Chicago. Pretty much the furthest Western suburb before you hit the corn fields that exist in the rest of Illinois. It’s a kind of a small town atmosphere. It’s got a little downtown area and good schools, good people good Midwestern values. And that’s where our office happens to be located.
Antoine Walter: And you’ve always been working from Plainfield, or did you move as well?
Jim Rieke: This area for sure. Our office moved a little bit. We had a originally our office was in Naperville, Illinois, which is the suburb just north of Plainfield. We had our r and d facilities in Plainfield, and eventually we built a new office building to be next to our r and d facilities and relocated there.
But yeah, for the last 30 years, I’ve been either in Naperville or Plainfield.
Antoine Walter: You mentioned the last 30 years, actually, that’s something really impressive in your path is that. You started as a commissioning engineer at HPD and 30 years down the line you’re director of process engineering and VP of Veolia Water Technologies. What did you learn along that path?
Jim Rieke: I guess it is kind of odd in our. Industry and generally in the world today for folks to be at one company that long. But it’s pretty common in, in my group. You know, we try to start our new hires in through our service and commissioning group, which is where I started, and that’s really the best to learn having experience in the field.
Directly with our equipment and our clients very steep learning curve,
Antoine Walter: What did you commission when you started?
Jim Rieke: the systems we design and provided mostly evaporation and crystallization systems. We’re a little bit strange in the Veolia world that Veolia focuses more water systems. I’m in the water division of Viola Water. But our group gets a lot into Production side of things.
Chemical, inorganic, chemical production, refiners systems of that nature. So, yeah, a lot of learnings in that area. And after the commissioning process I moved into our process design group. actually designing the the systems we provide and then transitioning into a sales group for a bit.
And then back to being the manager of the design group.
Antoine Walter: did the recent moves with the merger with SUEZ affect your role or do you have a broader Specter today or? did that change your life?
Jim Rieke: it’s another set of colleagues, I think and another. Set of technologies that are complimentary to ours hasn’t really affected my work too much. Other than gives us a little bit more flexibility in the systems that, we can offer by integrating and collaborating with the Sue technologies which, which are very complimentary to, Veolia’s Toolbox.
Antoine Walter: I have a muggle question. What does H HPD stand for?
Jim Rieke: Yeah, we get that occasionally. It’s goes back a while. H HPD was initially the Horton process division of Chicago Bridge and Iron. This was back pre 1970, and a few of the gentlemen in that company decided to split off and formed their own company. So that’s where H HPD branched off in 1970.
And we’re doing similar. things that, we did back then, just on a broader scale, and eventually, H HPD was acquired through a series of acquisitions into the V eolia family!
Antoine Walter: The reason why I wanted to speak with you today is that I’m conducing a lithium deep dive on the podcast, and I started a bit looking into the various value chains and there was one plant which popped up, which is the Naraha plant in Japan, I saw as. Plants that you’ve been developing and building for two 10 the story of that plant?
Jim Rieke: the Naraha plant is something that I’m personally very proud of, it’s a good success story for our company as well as, Orocobre who’s now Allkem. Combination of Galaxy and Orocobre formed Allkem a few years ago. The Miraja Plant is a joint venture between Alchem and Toyota TSU Corporation.
Toyota Lithium Company is tlc. They go by now that joint venture. we began working with or Cobra on this. It was probably five or six years ago now. Initially through our, testing facility where we demonstrated the flow scheme that they were looking to apply. And the plant is a facility that converts lithium carbonate to lithium hydroxide monohydrate. Allkem facilities in South America that produce lithium carbonate.
Lithium carbonate is shipped to Japan and through this facility is converted into battery grade, lithium hydroxide, monohydrate. So the entire process was developed by Veolia our group. As I said, we then did demonstration validation testing in our pilot facilities, which are also in Plainfield, Illinois. It’s a lot of close collaboration with the Ora Cobra people. Subsequently we entered into an engineering phase that was, it’s probably a year of feed engineering before the project was fully released. And Veolia the large company that we are, we’re fortunate to have a an entity in Japan that we work closely with but has some. Pretty good history of constructing facilities in Japan as well. So the entire facility then was designed and constructed and commissioned as a Veolia entity.
And operated?
The operation is by tlc the joint venture. That’s the plant started after some delays through Covid. We were getting ready to start actually last year, and then there was an earthquake in Japan which set us back a couple more months.
But toward the end of last year, the commissioning began. There was a slight break over the holidays, and then think we restarted early January the commissioning process, and by mid to late February, we were operating at greater than 90% rate. With on spec battery grade product, which is very impressive.
Antoine Walter: I think it is.
Jim Rieke: In this industry, you see other plants that sometimes have struggled to move through the commissioning process quickly, and I think it’s a good testament to TLC and certainly our commissioning group the the whole project execution team.
Antoine Walter: if I go back within that history, you said seven years ago you started working on the project, AK at the time comes to you and say, I have this brine. South America, which gets down, refined up to lithium chloride and if them carbonates, I want to convert that to Hydrocyte, so they take it to your plain field facility.
What is it that you have to test in your lab, and what is the treatment train which you end up building?
Jim Rieke: Sure. Yeah. Our lab is a really key tool in our design effort. In a lot of these flow schemes that can be somewhat unique usually will conceptualize the process flow scheme. in my group, the process design group and much of the unit operations that we use are fairly well known. The thing that is always unique is the actual chemistry of the lithium carbonate that Orocobre was producing, for example the expected quality of the lime that’s used in that process. So the testing facility allows us to validate process design that’s conceptualized and just make sure that the chemistry behaves exactly As we’ve anticipated and very important in the battery materials industry is the ability to produce, obviously the high purity product. So being able to understand how the impurities distribute through the system as you’re concentrating and purifying, is very important. And that’s something we’re able to do in the lab is very accurately flow sheet Chemistry and validate the process design. So we know that when we actually build the facility and commission it, that we’ll be able to achieve the purities required.
Antoine Walter: What’s this process? What do you have as steps which bring you from carbonate to hydroxide?
Jim Rieke: there’s a number of steps. the main overall process is using Lyme. To convert the lithium carbonate to lithium hydroxide. So the hydroxide ion is provided by the Lyme through the reaction with lithium carbonate. The lithium carbonate is reacted to lithium hydroxide with a byproduct of calcium carbonate.
So through the exchange of those ions, calcium carbonate is filtered, removed. And then you end up with a weak lithium hydroxide stream that also contains some of the impurities that entered with a lithium carbonate and with the Lyme that was used for the reaction.
that stream is further purified through ion exchange.
And then through a, an evaporative process, it’s concentrated and through a series of crystallizations of lithium hydroxide the impurities are removed from the lithium hydroxide. Lithium hydroxide is then dewatered and dried and bagged as a final battery grade product.
Antoine Walter: I’m right, the downstream portion of what you just described is the core of what H HPD does, so the evaporator, the crystallizer, probably also the dewatering. The first steps, so the ion exchanger, the chemical dosing of Lyme, is it also core technology from Veolia or is it stuff that source with partners?
Jim Rieke: It’s a combination of both. The reaction system the clarification. It’s something that our division is very familiar with and we designed those components. But you know, it’s technology that, can be procured separately from third parties. Certainly the centrifuges, the drying equipment are procured from third parties and integrated into the system. But we’re very familiar with designing and integrating overall processes. As you said, the main core technology for my group is evaporation and crystallization,
But we integrate those peripherals so that we can provide a system with a process guarantee around the entire plant.
Antoine Walter: So that’s one route to get to lithium hydroxide, which is this bride of Eva operation. And then you come with the refining. There’s another route which is currently developed. I’m not sure if there’s already a full scale of it, but it is to extract lithium from clays. And if I’m right, you have a project in the rail Ridge, so never with ion.
where are you in that project and is it comparable to what we just described starting with carbonate out of Bri?
Jim Rieke: Correct. Yeah. Yeah. We’ve been working with IIR for a few years now. Lithium from Clay has its own challenges. It’s a unique flow scheme. And again, the key is to concentrate the lithium and separate the impurities that are in the feed stack. So, with clay’s starting with their particular deposit.
There’s an acid digestion process. To remove the lithium and other compounds from the clay. And then that particular deposit also contains boric acid which Ioneer is intending to recover as a byproduct. through a series of, purification evaporation and crystallization steps the lithium is concentrated in a brine.
Separated from the impurities. And then a lithium carbonate precipitant is then removed from the brine and further purify to become a battery grade product. where we’re at with that project is we’ve currently done a testing and a, pretty good amount of engineering.
So it’s still in the engineering phase at this point.
Antoine Walter: When would you expect it to become commercial?
Jim Rieke: I’m not sure exactly the expected commercialization date, there’s still a probably a couple of years between the additional engineering and the construction process before, it’s started up.
Antoine Walter: So let’s take another route, which is, dare I say, the conventional route to lithium, which is to start with spodumene or lepidolite, whatever is in rocks, and then To refine that upt battery grade, be it carbonate or hydroxide. I was told that you were in Australia not so long ago, and Australia is known to be the place where we extract the spodumene and then we go down that route.
Jim Rieke: Correct.
Antoine Walter: Does that have a link to do I have to expect Veolia to have references and projects ongoing in spodumene? Do you already have some?
Jim Rieke: Yeah we’re currently in the, I guess, execution phase of one of those projects in Western Australia. There’s several companies that have built or are building refineries in that part of the world. From spodumene where there’s, you know, historically in, Western Australia, there’s been sp mean deposits that have been exploited.
A lot of that sp mean is currently processed in China, but in recent years there, SP mean is, intended to be processed locally and refined into lithium hydroxide. So, Albermarle Tianxi and covalent all have spodumene refineries in various states of construction and commissioning in Western Australia.
Antoine Walter: And Allkem just commission one. I’m just wondering because you’ve been working with Allkem in Naraha, so I was thinking maybe in Perth you might be also involved.
Jim Rieke: don’t know that Alcom has a spodumene facility. In Western Australia. I know they’re looking at some in Canada, which is another area where there’s sp But the company we’ve been working with in Western Australia for is covalent lithium.
Antoine Walter: how different is the process from spodumene compared to what we just discussed, starting from. Evaporation ponds.
Jim Rieke: sp odumene as you said, it’s an, or with, a couple of percent of lithium oxide concentration that spodumene conventionally is upgraded to maybe 6% as a solid through a benefaction process
Before it’s shipped to a refinery. Just to minimize the amount of.
mass that has to be shipped. But then the refining process involves crushing and cal signing to convert the lithium to a forum that’s leachable. And then there’s an acid roasting process where the lithium is, basically roasted and leached from the ore to form a lithium sulfate brine. That lithium sulfate brine is then through a series of purification steps purified and concentrated evaporatively. That’s where we get involved. And then after the evaporation process, when it achieves a certain concentration, it’s cost to size to convert the lithium sulfate to lithium hydroxide. usually that’s through the addition of sodium hydroxide. the lithium sulfate sodium hydroxide reaction results in lithium hydroxide and sodium sulfate. Sodium sulfate becomes a main impurity that’s removed with a crystallization process. the remaining lithium hydroxide is then crystallized a couple of times to achieve the desire purity.
So it’s a little different than the other process except the very end where, Lithium hydroxide is crystallized for that last purification.
Antoine Walter: You gave some keywords like evaporation and crystallization, which call for probably your proprietary technologies. How do you address that market like an OEM providing your Evaporators and Crystallizers, or as an EPC saying, Whatever starts from roasting up to the final dewatering can be done by us as an epc.
Jim Rieke: The real value that Veolia provides is the ability to understand the entire process and to be able to provide a system to I guess achieve the end goal from a starting brine, for example. So we’re able to provide all of the unit operations in order to achieve That technical goal and provide a process guarantee around that whole system. From a E P C standpoint you know, the construction side of things that’s not where so much, where Veolia’s value lies. Although we have in the past taken on E P C responsibility rather unusual. Our core value add is the system design and the supply of proprietary equipment that allows us to.
Achieve that that technical objective?
Antoine Walter: If I dare ask who’s living in that space with you? Let me try to name drop some Koch? Would that be the other big fish in that pond?
Jim Rieke: Yeah. I mean, Koch is somewhat involved in the lithium industry, but they’re more involved with, the EPC side and Some of the technologies but not as an extensive portfolio of technologies as Veolia.
Antoine Walter: So you would rather be working with them than be competitors?
Jim Rieke: yeah, and in some cases we are in the industry. They’re we’re somewhat complimentary to each other.
Antoine Walter: I’m trying to wrap my head around it. When I interviewed Ben Sparrow from Saltworks, he named spontaneously Veolia as the big dog.
Benjamin Sparrow: we do absolutely do have competitors.
There’s a certain very large and, reputable company out of France. Okay, so the Reds, . Yes. Yeah. And, uh, they equally like us practice industrial desalination. And with that, they’re a leader in CRC in lithium.
Antoine Walter: So I guess Saltworks is your competitor as well.
Jim Rieke: Saltworks more is focused on I think the technologies, the evaporation and crystallizations. So they play maybe closer in the space that we do, but they’re somewhat smaller company. And, again, I don’t think they have the range of technologies that, that Veolia does. That’s really what differentiates, Veolia is that we’re not only the big dog as Saltworks said in evaporation and crystallization and in the lithium world, but also the ability to just provide almost any unit operation required and integrate those all together to offer a system.
Antoine Walter: The reason why I’m asking is when I discussed with several consultants, what they told me is that, The bottleneck in that road. I mean that PowerPoint Road 2030 where we can maybe meet the lithium demand with some additional supply. The bottleneck might be on the refining part. And what some told me is that the order books are quite full in the companies like yours, which means that also the lead times will at some point get longer and it might become a challenge to deliver all of these plants worldwide. Does that. Depict your reality.
Jim Rieke: the challenge is quite large for the industry. you know, you’ve seen the amount of incentives that are being provided by various government entities and the announcements from almost all the automobile manufacturers.
That are planning to build EVs and have actually committed to a certain number of EVs by 2030 or 2035. So there’s gonna be a huge demand and there’s a whole value chain that’s required to support that vehicle production. So it’s designing and building the car manufacturing facilities. Designing and building the battery plants to support those vehicles. And going down a step further, designing the cathode active material plants to feed the battery plants. And then at the first part of that chain is the refineries to actually make the, materials. Lithium, the nickel the cobalt, manganese So I think, you know, it’s hard to see where the bottleneck might be, but there’s a very large challenge to all of those pieces of the value chain or the supply chain have to converge and be operational at the right time in order to achieve the end goal.
And certainly there’s building and commissioning and operating a refinery is gonna be part of that. Algebra, I would say to meet the supply needs. And yeah the supply chain for the refineries includes, you know, not only the engineering and supply of the systems the work that my company does, but also the sub-components that go into those plants, the centrifuges, the compressors, the dryers.
I think it will be a challenge to do all of that efficiently.
Antoine Walter: So what you’re saying is that it’s not one critical path with one bottleneck, but it’s a succession of different critical paths and potentially more than one bottleneck. So you have to really plan that out thoughtfully.
Jim Rieke: much so. And, you see the you know, the car manufacturers. On the end of that chain, getting very involved in each step through investments through equity positions, through off-take agreements. I guess to say again the algebra of that calculation is very complex and the planning required to make sure there are no bottlenecks.
So all of that supply lines up properly.
Antoine Walter: There are two more routes to lithium. One where I’m pretty sure you are involved and one where if I’m right, you’re not involved. Those two additional routes would be lithium recycling. And there, I think you already have active stuff ongoing. And the other would be direct lithium extraction where I didn’t see you having a footprint there.
is it right already and then maybe if we start with recycling, what do you do in that field?
Jim Rieke: Veolia has been involved with recycling? Veolia, it does have battery recycling plants.
And they are looking to further move up the value chain with those by not just recycling batteries, but also purifying the black mass results. And actually producing materials that can be reused cathode materials.
Antoine Walter: So does that mean that Veolia H P D is acting as a service provider to Veolia waste and hence upgrading the plan so that you can extract valuable materials from the black mess?
Jim Rieke: That’s the intention. We haven’t gotten to that point yet with Veolia, but Veolia HPD is active with other battery recyclers exactly that uh, lifecycle, for example. Exactly. We’ve supplied Evaporation and crystallization equipment to be installed in one of their hubs.
And that plant is currently under construction.
Antoine Walter: that’s one more route. And what about the D L E route?
Jim Rieke: The DLE route with Veolia and Veolia HP D group. have our own DLE technology, but there are many companies out there that are developing such technology and we are. Involved with projects where we would be engineering and supplying the equipment downstream of the DLE to take the upgraded lithium eluent that comes from those systems and further concentrate that purify it and crystallize either lithium carbonate or lithium hydroxide from that stream.
Antoine Walter: So you would be a post-treatment to DLE operators, which enable them to go to battery grade.
Jim Rieke: Correct,
Antoine Walter: You mentioned that you don’t have in-house technology for that. Yet Sues wts. So the portion of Sues, which is now part of Veolia used to be active with their membrane division and in several projects I crossed them in South America at least. Does that mean that it’s might become part of your lithium portfolio at some point?
Jim Rieke: it could be you know, I mentioned that earlier that Suez, and Veolia have a lot of complimentary technologies and certainly the former Suez as was very strong in the membrane area. So you see a lot of these flow schemes. Require or utilize membranes for that initial concentration of the lithium once it’s recovered from whatever resource is feeding the facility. you could see d l e becoming part of our portfolio, but it most likely just because it’s very specialized and sometimes specific to a certain feed brine most likely will be a third party. Unit operation that’s integrated into a Veolia facility or a Veolia design. And we would just provide a system that included that as a piece, but likely procured from a third party.
Antoine Walter: So, you know, I have this backstory project, which is a bit the start of my lithium deep dive, which is that. Just next to the Houma. I grew up there is a source of lithium. I make you read the short version of that story, in DAOs Brine, there is 300 to 400 And so I was wondering who would be the right people to address if I was to say I want to switch gears and I stop my podcast thing and I go really
Jim Rieke: is
Antoine Walter: a lithium extraction. So if I get your rights, I would need to look for a D L E company and you might be able then to supply me with a refining step.
Jim Rieke: Correct. Yeah. Four three or 400 ppm, lithium, without a d l E technology, it would be, probably uneconomical to try to recover that. But that’s the benefit of these D l e systems that have been. Developed in recent years is all of a sudden there’s much more lithium that’s available in the world to be recovered in an efficient way. So yeah, , that would be the likely path for you to develop your 400 PPM lithium source is a D l E provider that has a demonstrated technology. They would probably do a little demonstration plant to show that can be concentrated to say, two or 3000, 4,000 PPM through their technology.
And the d l E technology usually not only concentrates the lithium, but it also purifies it during that step. and then once that, brine is. Concentrated and purified a bit. That’s where Velia could take over and through the more conventional unit operations that we have in our toolbox put together a system that further concentrates, purifies, and ultimately crystallize and, produce either lithium carbonate or lithium hydroxide.
Antoine Walter: As you mentioned, this new development of d l E opens many new sources of lithium, which is great on one end, but if you are a developer , like me in that example, it means a lot of competition. Which also means I have to be fast to market. if I want to secure that, you can deliver me my refining step.
How early do I have to place a bid? And what is the timeline between the moment where we sign an agreement that you will refine my Lithium and the moment where it is commercially producing lithium in South Zes.
Jim Rieke: Oh, I would say The first thing that we always want to achieve as a, design freeze, a process design freeze. So you’ll see in a lot of these. Projects that we’ve been involved with. it takes six or seven years from the time we first make contact with the client to that commissioning process.
But a large part of that often is doing the design work testing that allows you to validate a flow sheet and achieve design freeze.
Once you have a frozen design. Then you can move that process into the detailed engineering phase, which then leads to procurement and construction. So from process design, freeze through construction to commissioning, that lead time is maybe two and a half years, I would say, as a typical, and I think as we through the industry. Have more learnings on, the different flow sheets that are available to move a certain brine or a certain clay or a certain hard rock a lithium hydroxide or a carbonate product. The more experienced the industry has, the quicker we can achieve that process design freeze.
Antoine Walter: So that is one aspect of the story. The other aspect of the story is that if you. Can extract as much value as possible along the process you probably shall do it. And you mentioned how there’s one byproduct, which is calcium hydroxide. Are there more byproducts along the re refining value chain? And how do you valorize those byproduct and how do you extract them?
Jim Rieke: Correct. Yeah. in these processes, there’s usually some byproducts just due to the chemical reagents that you use in order to convert the lithium to the final form that you, you wish to use, whether it’s lithium hydroxide or lithium carbonate. The byproducts that result it.
For example, in the Naraha plant, one of the byproducts is calcium carbonate. carbonate as its lime mud, essentially normally doesn’t have a lot of value. One of the unique things about the Naraha plant though, that again I think is something that could be applied elsewhere and it fits into Veolia’s corporate mission is Recovering that and recycling that.
So at the Naraha plant, the calcium carbonate is recals, signed through a lime kiln and converted back into active lime that can then be used at the front of the process. that’s one way, or one byproduct, and one way to valorize that byproduct in the spodumene path that we discussed. A byproduct of that process as sodium sulfate. Sodium sulfate is, it’s a commodity chemical that’s used around the world. A lot of it in the detergent industry for solid detergents. So there is a use for that. But with more and more of these refineries that are coming online there will be more and more sodium sulfate To utilize and the existing marketplace might be stress.
So there’s various processes as well that Veolia has to valorize sodium sulfate, one of which is a conversion of sodium sulfate to potassium sulfate, which is a specialty fertilizer one that switch is quite beneficial Compared to other fertilizers and that it’s low in chloride. So it’s better for the environment than conventional potassium chloride fertilizers. So that’s one path of valorization of sodium sulfate. And then Veolia is also has a technology that converts the sodium sulfate back into sodium hydroxide and sulfuric acid so that it can be recycled.
Directly into the plant and offset fresh makeup of those chemicals.
Antoine Walter: You just mentioned several technologies which you have in house. So I’m wondering if, now I take my business hat, what is the special sauce of Veolia? Is it this constellation of technologies that really you can address whatever part of the process you’re gonna have? Whether something in-house or the know-how to take a third party?
Is it the process warranty? You mentioned a bit earlier in the conversation, is it your ability to deal with. Complex and large project. If you have to name just one special sauce, what will it be?
Jim Rieke: Oh, that’s hard because it really is a combination of things.
Antoine Walter: Let’s go for the combination.
Jim Rieke: let’s go over the combination then. Yeah, I, well, I think firstly we have, you know, very smart people that, work at Veolia with a wide range of experience in the chemical processing industries.
So we are able to put together these rather complex processes that, you know, often are first of a kind or have very unique feed stocks. we have the unit operations in our toolbox that we understand very well. So we’re able to put those systems together and optimize those and as well as having the testing facilities to validate those systems and provide process guarantees.
And then we’re a large enough company as well as Veolia to be able to, those systems that are often, 40, 50 million systems we can provide them on a global basis with the full backing of Veolia. process and mechanical guarantees, which is very comforting to our clients, especially some of these players in the battery markets, for example, are smaller companies.
So being able to get those projects financed is a lot more feasible when you have someone like V eolia Providing the process designed.
And then, you know, the capability to do that and look at all the systems holistically, like at the Na as opposed to having a separate third party, maybe an EPC that doesn’t understand that technology, have to put all of those operations together. It just allows us to Provide a more holistic offering and to control the risk a lot better for ourselves and for our clients.
Antoine Walter: Let me try to see if I get that special sauce. so you have people dealing with complexity. That’s one first element. You have the tools in toolbox. You have the testing capability, which enables you to then take process quantities and then you are large, which means that you can be really everywhere worldwide, which makes it easier to finance a project, and your engineering in-house gives you a holistic approach.
Jim Rieke: it’s a pretty good summary. Yeah. Yeah. Thank you.
Antoine Walter: the testing? Does that mean that every project has to come , to plain field at some point, or do you also use the full Veolia network to tap into other facilities?
Jim Rieke: We do use the Veolia network. To tap into other facilities in whether it’s, you know, we have a very strong technical and development group based in Paris that we interface quite a bit with. And now we have the former SUEZ company also has very strong testing capabilities, more on the membrane size that we’re collaborating with. But yeah, when we’re doing. Complex flow sheet development, and most of that for the battery market industry is in Plainfield. But not all of that has to be tested. It’s only when there’s a gap in our understanding or a special chemistry that we’re not familiar with that, we’ll wanna do some validation testing.
Antoine Walter: What is the size of V H HPD today?
Jim Rieke: Our group is about 200 people. There’s about 150 located in the Plainfield office, and we have another satellite office in Bilbao, Spain that has similar capabilities but we collaborate very closely and they just geographically are better able to service the European area.
Antoine Walter: And what would be the turnover that business unit of 200 people?
Jim Rieke: turnover is, you know, 150 to 200 million per year.
Antoine Walter: that makes for a good tour of your word at Veolia HPD. So really thank you for the openness. And you didn’t. me back on any of my tricky questions. Even when I tried to figure out what we were doing in Australia, which maybe was secret, apparently, hopefully not.
Jim Rieke: No, I mean, Australia, there’s so much going on and there always has been in the mining industry, especially in Perth it’s like a, center of mining activities. So number of things happening out there, a number of potential clients, and we’ve had a big presence there for many years.
Antoine Walter: Well, thanks for that deep dive, if that’s fine for you. I propose you to switch to the last section, which is the rapid for questions.
Jim Rieke: Okay.
Rapid fire questions:
Antoine Walter: So in that section, I try to keep the question short, and you are supposed to keep the answers short, but you can also take more time on never cutting the microphone.
And you’ll notice that the one which is always sidetracking is me. My first question is, what is the most exciting project you’ve been working on and why?
Jim Rieke: Yeah, I think we’ve covered this. The most exciting project has been the Naraha plant, you know, just because it’s the, I guess, the most recent one that started and the commissioning went so well when I think it’s a great story for the industry. How quickly it started. I’ll say there’s a close second.
We’re working with energy Source on a project in California which is a D L E project that’s removing lithium from geothermal brine. And Veolia would be providing all the downstream equipment there as well as for that particular facility, operating the facility. So hopefully will be commissioned in a couple of years that we’re just moving into the construction process hopefully soon.
Antoine Walter: California, is that the Salton Sea or is it another project?
Jim Rieke: Salton Sea. Yes, correct.
Antoine Walter: Okay. I heard that’s the most tricky one and you solved it.
Jim Rieke: Yeah. The tricky part I think is managing the geothermal brine which, you know, has very high temperature. It has some scaling compounds. The good thing about that facility is Source actually operates and has operated that plant for a while and knows very well the characteristics of that brine.
And they’ve developed their own d l E technology, which is you know, they have a long period of demonstration on that particular brine with their technology. So I think it’s after you get through the dle, the downstream part is more conventional equipment that. Veolia is very good at providing
Antoine Walter: I warned you about the sidetrack, sir.
Jim Rieke: Yeah, I know.
Sorry. And I’ll talk a lot too, and so we can get ourselves into trouble.
Antoine Walter: I have one more in the sidetrack, which is, you mentioned Canada and there’s this mining area around Quebec and basically not so far from playing field. Is that something you’re looking into?
Jim Rieke: Yes. Yeah, it is. we have a couple of clients up in that area as well in That we’re in, in, I guess, various stages of the project with for sping conversion from those facilities. And that Beckon core area up near Montreal is very active. Not only with. Refining, but also Cam p cams.
And again that’s I think the Quebec government trying to incentivize that sort of activity.
Antoine Walter: Sorry for a set for the sidetrack. Let’s go back to the main track. Can you name one thing that you’ve learned the hard way?
Jim Rieke: Through my career. The things that are, the big learnings are the hard learnings. You know, the ones that may be a little bit painful, and these often happen during commissioning process. But I guess o one key learning is that it’s usually not the things that you are worried about that trip you up in, in these complex flow schemes. Sometimes they’re rather simple things that, cause the most delay or heartache. So it’s really kind of makes you focus on being very thorough all aspects of these projects and not just the ones that seem to be the most tricky.
Antoine Walter: I think that’s a very valuable one. Thank you. Is there something you’re doing today in your job that you will not be doing in 10 years?
Jim Rieke: That’s a good question. Probably maybe I won’t be typing as much. I think with advances in, in technology. But otherwise, I, you know, I don’t know that my job’s gonna change too much in the next 10 years, and I think That’s what I like about it. There’s a lot of variety and with chemical engineering and you know, building these refineries it’s basic principles and, you know, the equipment will be similar.
You know, maybe the technology that allows us to the engineering more efficiently or communicate more efficiently will be different. But I think more or less I’ll be doing mostly the same things.
Antoine Walter: What is the trend to watch out for, be it in h HPDs core sector or in the water sector more broadly speaking.
Jim Rieke: Trend to watch out for. I think you’ll see more focus on recycle and recovery of these byproducts. I think that will become more evident thing that needs to be addressed as some of these plants start to be commissioned. And those byproducts need to be valorized somehow or disposed of. And the trend, I think will be to, vary with a lot of focus to try to avoid disposal and to instead find a way to, to recycle or reuse.
Antoine Walter: I really want to prevent starting a new sidetrack here, but it’s a fascinating one, which we’ve discussed several times on that microphone, because having the technology to recover a byproduct is one thing, but you need to create the value chain and to have full system in place so that once you’ve recovered something, it’s the ones you mentioned like potasium sulfate or sodium hydroxide, that then you can.
Really bring them along that path, and I guess that’s the thing we have to build going forward. If we want to go into this circularity.
Jim Rieke: Yeah, correct. It’s another one of these challenges where there’s some algebra to be done on how to make it all work in an economic fashion. But, the drivers will be there, I think, and I think society will demand it as well. So, you know, it’ll be a combination of the refiners The battery manufacturers the car companies all will have to to make that a priority and to find those I guess the, path to market to reutilize those byproducts.
Antoine Walter: Last question, would you have someone to recommend me that I should definitely invite on that microphone as soon as possible?
Jim Rieke: Boy, that’s a tough one. I would try to get maybe someone from one of the higher up the value chain, one of the people from a, one of the car companies perhaps would be interesting, I think, to see how they’re, how they see the. The marketplace and their activities through that value chain that we discussed previously and how they’re involved throughout those steps.
Antoine Walter: sent a Twitch to El Musk, but he wasn’t available. Huh?
Jim Rieke: That would be a key. Yeah, if you could get him on the show, that would be great.
Antoine Walter: actually all jokes aside I just looked at the valuation of several lithium companies and you have a couple of them which are valued at roughly the same amount than Twitter and would I have been in his shoes? I would rather have both one of these companies than Twitter, but I’m no one to do and I’m certainly not in his shoes, so, yeah.
Jim Rieke: Well, I, you know, it’s funny you mentioned him if you have a, an opportunity, they just I guess publish their master plan three which I think Tesla does occasionally they’ll talk about, Not short term goals, but some of the longer term objectives. And, I think Tesla does plan to be more involved in that supply chain as a, producer of EV cars wanting to make sure that they have a secure supply of cathode materials. That’s. I think they’re very focused on, on that side of the business, so that, that would be a fascinating discussion. But I think all the other car companies are thinking similarly just in order to secure the commitments that they’ve made five, 10 years from now to produce those cars.
Antoine Walter: Makes sense. Well, Jim, it’s been a pleasure to spend that hour with you. If people want to follow up with you, where shall I redirect them? The best.
Jim Rieke: Yeah, they can contact me on LinkedIn or through email at@jim.rickyviola.com.
Antoine Walter: I’ll put the links to both your email and your LinkedIn profile in the show notes. So if you’re listening to that, just go have a look at the show notes and you’ll find everything there. Well, thanks for your time and I hope to get to speak to you again in the future when you commission your first D l e refining plant, because that might be the reference I have to visit for my own project.
Jim Rieke: That would be great.
Antoine Walter: thanks a lot.
Jim Rieke: It’s been my pleasure.
1 thought on “How ‘Reverse ZLD’ made the World’s Largest Water Company a Lithium Refinery Expert”