Ready for an epic journey? Strap in as we rock’n roll from deep-down brine to powering our future through lithium! We’re plunging into the buzz around Direct Lithium Extraction and companies like Standard Lithium who are making magic happen. Water and lithium – it’s a wild ride, let’s follow our guide this week:
(Find out more with my entire Lithium deep dive.)
with 🎙️ Andy Robinson – President and COO of Standard Lithium
💧 Standard Lithium coins itself America’s 21st century Lithium Company. They’re expected to become the first lithium developer in the World to produce direct-extracted lithium at a commercial scale in El Dorado
Slider: The 5 Rules to Successful Direct Lithium Extraction
1676114_Lithium-Slider-6_072423What we covered:
🌊 How a bromine plant in Arkansas is being converted into a lithium extraction mine to create a revolution in lithium production
🔋 Why lithium plays an integral role in clean energy initiatives, powering everything from electric cars to grid storage
💡 What challenges are faced when extracting lithium from natural brine, and how innovative companies are overcoming them
🌍 How Standard Lithium is integrating sustainability into its lithium extraction process to make it more environmentally friendly
⚙️ Why Direct Lithium Extraction (DLE) may become the preferred method in the lithium industry, potentially shaping the future of the sector
🚘 What role lithium plays in the electric vehicle revolution, and why is it indispensable for battery production
💰 How we can exploit the significant financial potential of lithium production, as hinted at by industry leaders like Elon Musk (which I may still have outsmarted)
🔄 Why a full disclosure of the entire flow sheet, from resource to end-product, is essential for building investor confidence in lithium extraction
📈 What the future of lithium demand looks like, and how production companies are preparing for a potential structural deficit of lithium chemicals
🌱 How the incorporation of carbon capture technology into lithium extraction processes reduces the environmental footprint and promotes a more sustainable industry
🧪 How continuous chemical processing redefines lithium extraction methods and raises industry standards
💼 What the key factors considered by Standard Lithium are when identifying potential lithium extraction sites
👥 Why stakeholder approval and local government permitting is crucial for the success of lithium extraction projects
🏭 How the use of existing infrastructure in Arkansas simplifies the permitting requirements for new lithium extraction plants
🛰️ What a day in the life of a lithium extraction plant looks like, and what’s the path of lithium from entry to final product
🔥 … and of course, we concluded with the 𝙧𝙖𝙥𝙞𝙙 𝙛𝙞𝙧𝙚 𝙦𝙪𝙚𝙨𝙩𝙞𝙤𝙣𝙨 🔥
Resources:
🔗 Come say hi to Andy on Linkedin
🔗 Check Standard Lithium’s website
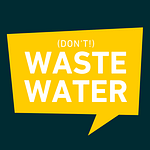
is on Linkedin ➡️
Teaser
Table of contents
Key Take-Aways
This interview of Antoine Walter with Andy Robinson discusses the extraction and processing of lithium, specifically from brine water, which is commonly found in certain geographical locations like the Smackover Formation. This discussion provides a comprehensive overview of the lithium extraction and processing process that Standard Lithium is developing. Here are the key takeaways:
- Lithium Extraction: The technology developed by Standard Lithium leverages the existing infrastructure and operations of a bromine extraction plant. The bromine extraction process already pumps a large amount of brine from the ground, which happens to contain lithium as well. Standard Lithium’s technology takes this brine and extracts the lithium from it.
- Extraction Process: The extraction process relies on a sorbent material that selectively absorbs lithium from the brine. This sorbent is designed to release the absorbed lithium when exposed to a simple sodium chloride (table salt) solution, allowing for the recovery and subsequent purification of lithium.
- Efficiency and Sustainability: The process has demonstrated high efficiency, with 88% lithium recovery from the brine. It also operates at low temperatures, which helps to minimize energy consumption. Furthermore, the lithium extraction process can operate continuously, unlike other methods that require batch processing.
- Challenges: Challenges encountered in the process include handling natural brine, which can behave unpredictably and differs significantly from synthetic brines used in lab settings. Moreover, financial and regulatory aspects present additional challenges. For instance, in Arkansas, they are not allowed to sell the lithium they produce until a royalty structure has been established for the mineral.
- Future Developments: The interview also discusses the possibility of additional projects such as carbon capture and the conversion of lithium chloride to hydroxide. The ultimate goal of the company is to create a “responsible” lithium product that supports the transition to cleaner energy technologies.
Editorial
It’s now several weeks that we’re exploring together the depth of the lithium World, and we’ve heard quite a lot of things about Direct Lithium Extraction, or DLE. For instance, we’ve heard from Cris Moreno, the very recently-appointed CEO of Vulcan Energy Resources how: DLE is already commercial and accounts for 10% of the World’s Lithium.
And yet, you’ve heard many of my other guests on that microphone discuss with me how DLE is not yet commercial, and might be the next big thing, assuming it gets to that commercial scale. So where’s the truth?
Well, everybody’s right here. What Cris Moreno refers to is that in Argentina and China, companies have been using DLE as one step of the lithium extraction process while still leveraging evaporation ponds as a sequel step.
What’s still not reached yet, though, is a company or process that would be leveraging DLE and getting rid of evaporation ponds. And that is the game-changer that would unlock many more geographies and resources across the World, hence the legit excitement around it.
Now, excitement often comes as well with wide-ranging creativity, and right now, the DLE scene is blessed with blossoming companies trying out a wide range of technologies, let’s face it, it’s also because of that, that the lithium field is so thrilling for a water nerd like me.
But before further exploring these technical takes, I thought it would be worth following Ben Sparrow and Robert Mintak’s advice and getting Andy Robinson on the microphone. Why so? Well, because if Standard Lithium is set to be the first company in the World to bring DLE to the commercial scale, without any evaporation ponds, it’s probably because of him.
As you’ll hear in a minute, he won’t admit it, and he’ll refer to luck, as Robert Mintak did before him. But still, from picking the right place to go all-in on DLE, to testing out a bunch of processes from lab to demo-scale continuously over the past three years, to the next steps on the horizon from lithium carbonate to hydroxide conversion and to carbon capture, it takes a sound methodology, and a cool head approach, which can probably inspire many in that field.
So without further due, let me leave the floor to Andy, to explore his 5-step rule for a good lithium project and learn from his learnings in El Dorado.
Full Transcript:
These are computer-generated, so expect some typos 🙂
Antoine Walter: Hi Andy. Welcome to the show.
Andy Robinson: Thank you, Antoine. Pleasure to be here.
Antoine Walter: I cracked you the secret of it before starting. You have been warmly recommended by two of my very recent guests, so I have high expectations for today’s discussion, and I’m pretty sure you’ll be able to outperform those expectations.
So before I jump straight into the topic, let me start with my opening tradition, which is the postcard. What can you tell me about the place you’re at, which I would ignore by now?
Andy Robinson: I am currently located in Vancouver in North Vancouver, which is a lovely part of the world. I’m not from here originally. I am an Englishman by birth. But I’ve lived here in Vancouver now with my wife and family for 17 years. We’re longtime residents here in Still love coming back home to Vancouver every time I travel to various parts of the world. It’s an amazing part of the world to come back to.
Antoine Walter: I told you that you came in warmly recommended. Let me just let you listen to what Robert Mintek told me. So how does one get in the top two in lithium extraction globally?
Andy Robinson: Hard work and time served to be honest, Antoine. I’ve been working with Robert now since 2014, so we have a long track record and through that entire history of working in the lithium industry, we’ve been solely focused on using modern extraction.
Processing techniques to get lithium out of an existing resource that has being processed and developed using conventional brine evaporation techniques. So that was in the Clayton Valley in Nevada and the us and then since, 2017 onwards working in the smackover formation in Arkansas and more recently in Texas to, trying, testing, breaking every single type of, lithium extraction technology that’s available.
Creating our own using other people’s, et cetera and really just spending the time. The bench scale and, in the laboratory literally sort of test tube beaker scale right the way through to, where we are right now, which is a very large demonstration plant, which runs 24 7 in Arkansas.
And just about to, moving towards commercialization, like making it even bigger again yet. I would argue with Robert, whether I’m one of the experts we’ve just been lucky. We’ve surrounded ourselves with really smart people they’ve done all the hard work.
I just get to tell people about the work that they’ve done, frankly.
Antoine Walter: That’s an interesting pattern. I think Robert mentioned 15 or 20 times during my conversation with him how lucky he has been so. maybe you are very lucky the two of you, or maybe there’s a bit more than luck involved in what you’re developing in El Dorado. I’m really looking forward to dive a bit deeper into that.
Before I’ve listened to your appearance on Joe Lowry’s podcast, and I’m a water guy, so I had to get myself educated to this lithium word. So jewelry has been my primary source of getting that starting point , in understanding that the lithium and it keeps repeating that lithium is not a commodity, it’s a specialty chemical and it is a very special field.
So
What’s your position there in the sense of really breaking new grounds? You might be leveraging stuff which exists for a while in terms of mining, exploration, stuff like that, but you’re also creating a full new category within all of that.
Andy Robinson: Yeah. I mean, the lithium world is a very rapidly evolving industry. for many decades it was a very niche industry with a very small number of players and processing techniques. And the products that they made were, very carefully tailored.
The entire industry is undergoing, a revolution frankly, in terms of the amount of lithium, which will need to be produced over the next several decades to enable electrification and energy transition story, which is happening around the globe. And the role of suppliers such as ourselves, the standard lithium, and the people who will use the lithium products that we will be making, that’s also gonna need to evolve Antoine types of materials , that we will make from the lithium contained within the smackover formation in Arkansas and Texas.
That’s gonna be used to fuel an entire new generation of vehicles stationary storage facilities, et cetera. And so, Joe is absolutely correct , that lithium currently is not a fungible good. It’s not an instantly tradable commodity. It is still very much a material is made by a producer and then it is qualified and used by an end user in their particular process, whether they’re making cathode materials or whatever they’re using the lithium chemicals for.
So there is still very much a bios seller, relationship, which is not, there again, a normal sort of commodity type relationship. but it, will evolve. I’m not. Really not going to sit here and try and predict where that relationship will sit in five years time or 10 years time, other than say, our function, the standard lithium, is to find resources, build the technology , to extract those resources and turn them into a very high purity end product that, potentially can be sold to multiple different eventual consumers of that product.
there’s a long way to go Antoine in the industry as a whole. It will evolve and develop over the next few decades for sure.
Antoine Walter: You mentioned your project in the smackover formation. If I’m right, you are the person who pointed that place and said, that’s where we have to go. So what indicated you that was the best place , to start that journey and what were you looking for? What were these indicators? Which put you on the way?
Andy Robinson: there’s a couple key things there. One is clearly indication of grade. So whilst we are, you are right, we are a water pro processing business. It’s still, has to have a mining mentality. And as, as with almost everything in mining great is king.
The concentration of the thing that you want to get out of the stuff that surrounds it is still extremely important because it’s a very fundamental lever on the economics of extracting that particular material. So grade is very important and there was a wealth of historical data throughout the smackover formation that pointed towards a very significant lithium grade contained within the brines.
So there was enough data there to point that, okay, grade looks to be very favorable there. The other aspect and again, I think this kind of came from Robertson mine experience working in the Clayton Valley in Nevada, was that size of the resource is also fundamental. A very small high grade resource could be good, but it’s not a great, story to tell when you’re trying to build a large company like, Robertson, my.
Job and ambition is to build a very large Lithium producing company, , the North American market. And so you need a very large resource. And certainly the scale of the smackover, I think is completely unparalleled, more or less anywhere else on the planet. To the best of my knowledge, it truly is a gargantuan resource.
The other thing then is a little bit more arcane and a bit more technical, which is I’ve spent a large amount of my sort of professional career working in and around groundwater resources. And so I always whenever I think about how to envisage a fluid based resource, I always given a preference, would want it to be in a porous media formation rather than a fractured media formation.
That means the distribution of the resource, the way at which behaves when you induce a pressure gradient on it, when you try and pump it or put it back into the formation in a porous media, it’s much more predictable. You can understand how it will behave over not just days and years, but decades and centuries potentially.
And the smack over formation again is geologically fantastic in that regard? Because in the key horizon. It’s almost a perfect lytic limestone. It’s just this beautiful granular, porous medium that behaves very predictably. And therefore, when we think about resources it’s much easier to understand and to predict its behavior.
So those are some of the aspects as a project developer, We always think about permitting stakeholder approval. How receptive are the people who live in the area and actually own the resources? How amenable are they going to be to people turning up from Canada, particularly people with funny accents like mine saying, Hey, we’d like to do something in your backyard.
And southern Arkansas and East Texas certainly tick the boxes there for us as places. , there’s certainly open , to resource extraction and processing type industries cuz there’s so much of that goes on there. And then one of the reasons that we also kind of ended up where we did was that there’s this amazing history of brine processing in the area in southern Arkansas.
There’s this , hidden industry that even most people in Arkansas have no idea is actually there. But you know, 40% of the world’s bromine comes from the smackover formation, brines. And so there’s this very well established regulatory environment where it’s well understood that you can drill a hole, drill a well into this formation, you can pump a brine solution to the surface.
You can extract a mineral, historically in the case it’s been a bromide ion has been removed to make elemental bromine. And then you can put that same bromine less or bromide less brine back into the formation again. And they’ve been doing that for six decades. So it lends as a very high degree of stakeholder and regulatory support.
Where people are just familiar with the concept that, oh yeah, you’re gonna pump something out, extract some value from it, and put it back it where it came from. Yep. We’re good with that. lots of those. Aspects came together , in the smackover formation. That’s, that was really what drew me there.
And when we formed the company and got it going, that was front and center of where we wanted to be. And I’m still very excited to be there for sure.
Antoine Walter: if I get you right, that ticks five boxes. You have the grade of the resource, you have the size of the resource, which is huge. You have the fact that you understand the underground and that it’s a porous material which gives you a good understanding of how it flows underground.
You have the permitting, which is especially in lengths as or dissolved because they’re extracting that brine, which also links to number five, which is this processing of the brine already happening. So you have all that context to extract lithium, but at that stage, you’re still not. Extracting anything, you’re just tick boxes.
So what I’m interesting is how do you go to the next step, which is, I guess I’m not a big specialist, but in was pretty impossible to have Evaporation Ponds, that was lending itself to D L E.
Andy Robinson: absolutely. Yeah.
Antoine Walter: But how do you pick the type of D l e, which you ended up
Andy Robinson: Yeah, this is also one of the central tenets of when we formed the company. So yeah, you really nicely laid out sort of those five key factors when we think as a project developer, like what, as a lithium project developer, what do we wanna see there?
But when we think about the D L E technology, the philosophy was always not, I know the best technology. Like I have found an amazing D L E technology and I’m going to make it fit in the smackover formation. It was always very much okay. First of all, we’re always gonna work with real brines.
I’m never gonna do the work with synthetic solutions. And we will effectively at the start, I think we’d be very open. It was, let’s throw everything against the wall and see what sticks. Because there are so many different ways that you can think about selectively extracting lithium from a continuous brine stream.
And so we honed in we tried lots of things and lots of things worked. You can get a lot, right? You can make almost anything work at a bench scale. So almost all technologies look fantastic on the bench scale for the most part. But we applied a critical eye to those ones.
We found ones which seemed particularly well suited to the smackover formation brains. And then we adapted, adopted optimized and de-risked. So we went through multiple. Technologies, which looked to work we then started to scale test them at larger scale. And we kept an open mind all the way throughout.
And that really was, the process that we went through. and the key thing for us, Antoine, is that, D L E is really just a name. A philosophy given to, what’s being contemplated in lithium extraction, really what we are doing is continuous chemical processing.
D L E in my mind encompasses absolutely the entire flow sheet, frankly in a lot of sort of d l e providers, it’s just kind of one unit operation inside a multiple unit operation flow sheet. In my mind it’s an integrated chemical process from the start to the finish.
And that’s been very much the attitude that we take and that’s why we spent, frankly, a lot of money of our shareholders money when we designed and built this large demonstration plant and installed it. El Dorado, it was a relatively aggressive, bold move , on our part.
We spent a lot of the money that we had available to us as standard lithium at the time to do that, but it was absolutely so that we could try to integrate a continuous flow sheet at that plant using real brine every single second of the day. And maybe we’ll get into this a little bit better, but the difference between running processes in a laboratory, even when you sort of do some scale up or in a 40 foot ccan somewhere where you might run a process for a week or two and then, you’ll swap over your feed, et cetera, to then actually running a real continuous process with the real brine that you’re gonna be processing in the commercial plant.
Those are night and day. They genuinely are. There’s a lot of learning that takes place in those smaller piloting type operations. Not to say they’re not worthwhile, but the difference in learning and understanding between those sort of smaller, more discreet batch processing style operations versus running something and running millions of liters of brine through it on a continuous basis.
And that’s real brine, which Natural feedstocks vary over time. Like you see changes even, at a core scale, they look very similar. You still see variations and those all have processing implications, which are not always apparent when you’re just running small amounts through for a kind of a short period of time.
Antoine Walter: there’s one specific question I have on that part, which is this upscaling when you go from the pilots , to the demonstration plant where you’re running, not at the commercial scale, but still continuous,
Andy Robinson: Yeah.
Antoine Walter: Is there an unexpected source of pain?
I mean, you might be controlling the process, but all of a sudden , there might be like a boring part, like ensuring that water flows.
Andy Robinson: yeah.
Antoine Walter: not exactly what you would be looking for in a pilot, but still that’s the hygiene factor is, and maybe. That might be on the critical path. I’m trying to find out what is the most unexpected, overlooked, touchy part, which can be troublesome when you go from pilot to demo.
Andy Robinson: some of them are extremely mundane. And some of them are, a little more chemistry focused. there’s a whole series. Thinking about sort of the chemical side or the process side. Those elements which are present at what would seem to be very small concentrations or very low concentrations can cause all sorts of unpleasant side effects , in your process.
And whilst they are not wholly unexpected, the way in which you actually have to deal with them, never the same. So they are the usual bad actors in any sort of water or brine processing operation. And they’re the same, things that cause all of the issues in produced water management at any oil field or gas field around the planet.
But they’re things such as silica, iron, manganese sulfur compounds, et cetera. , these things are present at low levels in almost every natural brine feedstock. And where you are riding a continuous chemical process, they have an effect. And so understanding exactly what effect they will have and it may not be on the lithium extraction part, it may be some other part of the flow sheet.
Understanding the real effect of those is hard to estimate ahead of time and problematic and challenging to deal with, to actually create a solution that will work at the commercial scale. Because again, these are things that you have to deal with on a continuous basis.
They are always present and they’re always slightly fluctuating, and therefore you need a flow sheet. And so you do see a lot of other people involved in this field who you’ll see them say, oh, these are the normal contaminants. We’re just gonna use industry standard processes to deal with them.
And whilst, on the face of it, that is true the practical reality of that is it’s still quite complicated and challenging to figure it out. And you have to figure it out before you go commercial. Like otherwise, your plan will not work. So that’s one of those sort of the chemistry aspects on the sort of the more mundane side.
Managing suspended solids is always an issue. It again sounds incredibly simple and straightforward. Hey, you just filter it. it’s not that simple and straightforward , in the real world on a continuous basis. So that’s always a challenge. And then one of the other aspects is whichever technology , you would end up using whichever combination of unit and process operations that form your flow sheet.
There is a lot because you’re constantly processing flow with changing chemistry all the way through your flow sheet. There’s a lot of instrumentation, monitoring and control, and you’re in an aggressive environment like you are dealing with a fairly hostile brine. And in our case it’s relatively straightforward and it’s chemistry, but you still have to control the process and things like, Sensors, pumps in line, online measurement, et cetera, all play a role in process control.
And so building a robust flow sheet where the control systems don’t get fouled, where you can control flow rates, pH, conductivity, timidity, all of those things in real time, cuz you need to understand those things to build an operating chemical process. Those are also things that go wrong a lot.
And so we’ve spent a lot of time figuring out, okay, what equipment actually works in this environment? And again, it’s not what equipment works for a two or three week campaign of testing. It’s what equipment works day in, day out for almost three years now. We’ve been really lucky, right? So because we are effectively piggybacked into Xi’s operations, they have six decades of operational history in processing brines from the smackover formation for bromide to bromine conversion.
So there’s a lot of institutional knowledge there from the people who work on those facilities that’s been, we’ve been able to benefit from as well. So we know what pumps work, we know what sensors work, et cetera, et cetera. We’ve been very fortunate to benefit from a bit of a brain trust in the existing brine processing industry in southern Arkansas.
Antoine Walter: funny cuz I can’t tell you from the lithium end, I can tell you from the water and maybe dirty water end, everybody always thinks it is possible to standardize and to have stuff which works like everywhere and to have industry standards. And then you figure out the hard way that it simply doesn’t work that way.
And that every single water metrics is specific and you need to adapt to that. So I guess if that’s true for generally speaking slightly dirty waters, it might be even more true with quite complex metrics is like, like the ones which you are leveraging there. You mentioned you threw everything against the wall and you saw what sticked, and you also said that actually a lot of it sticked.
So you could have taken all the processes, I guess you’re really chosen, best suited one, which at the hurt of it is an absorption. And you’re using if I’m right acemic absorbent. How do you end up with that? what decided you for that is strictly performance. So is there also an element of how reliable it is?
How proven it is? And I was discussing, I don’t know if they are your competitors because it’s really the other end of the world with Vulcan, which is developing this asset in Germany. And they are leveraging a different type of absorbent, more the live and style absorbent,
Andy Robinson: Yeah,
Antoine Walter: but they also patented their own version of the absorbent and they made it their atory process.
Do you do something similar? And because that was only seven questions, let me a eight. Why?
Andy Robinson: yeah. I mean, we’ve trialed and we’ve continued to evaluate other technologies in the demonstration plant, particularly, the D l E core. And when we’re selecting materials for use in the lithium extraction part, we are concerned with fouling.
We are concerned with how the lithium cell activity over time is also extremely important because One of the real benchmarks, if you like, of whether the process works is not necessarily the total capacity of the lithium absorption on your material, but how selective it is versus all of the other materials that you do not wish to carry through your flow sheet.
in our case, we’re in a very calic Brian, the Brian is hosted in the limestone, right? So we have a very calic brine. So it is, how does the material select for lithium against calcium, against sodium not just for 10 cycles, but for hundreds or thousands of cycles. And so because the material has to have longevity.
every material that you select and most of the materials that you looked at, whether they’re proton, activated, deactivated, whether they’re IOL materials , like the Livent material they all have fantastic performance out the box. They all look amazing in the first few cycles.
And then eventually you see capacity performance always asy totes. This is some sort of baseline performance over after 10, a hundred thousand, 2000 cycles. And so you need to use a material which behaves the same in a predictable manner, cuz you have to run a chemical plant.
at the commercial level. You need to have a process which basically does the same thing every minute of the day. Because you need a team of operators , to operate that. You can’t have a team of, 200 scientists constantly tweaking the process to make it work for the brine feedstock, you have to have a consistent brine coming into your plant.
And you need a process that a team of operators can actually work. They can run the plant and the process will not take care of itself, but it has to keep on doing the same thing day in, day out. You can’t have something that works one day and then doesn’t work the next. So the choice of material that’s certainly guided a lot by, does it work over the long term?
Antoine Walter: And so that’s ceramic absorbent. You’re leveraging. Is it yours or is it something you’re taking from the market?
Andy Robinson: It’s been leveraged off academic knowledge. We have made our own materials and we’ve also been using materials which are available out of the market as well. So there’s a kind of a combination which is which is in play at the plant. Yeah,
Antoine Walter: When it discussed with Ben Sparrow he theorized that as generation one and generation two, generation one being the one which you can backwash with water and generation two being the ones which you can backwash with assets. So you are generation two. When I proposed that theory , to Robert he was a bit more nuanced.
Andy Robinson: yeah.
Antoine Walter: where would you sit?
Andy Robinson: Yeah I’m not sure I’d fully buy into that because I think the Generation One materials, and I’ll, be clear, we, have been trying and successfully also using some generation one type materials in the plant as well. Again the difference between like you were saying with regards to Vulcan, like using as you describe it, a Livent-like material, which is a layer, aluminum, sort of hydroxide type material that has been modified and adapted many times successfully over the last few decades.
So I think there are now some very clever adaptations that have been made as to how that material is The form factor, how it’s packaged, like what resins it’s kind of placed into. All of that sort of way in which it can be applied has certainly evolved and changed. And then again with sort of the ceramic materials, like whether our, we’ve been using a Titan eight based material and there are manganese based materials, et cetera.
They all have their strengths and weaknesses. I wouldn’t say one is necessarily better than the other. the layered methylate structures like the Titan Eights and the Mangan eights certainly have higher capacity. But they have pluses and minuses as well. They’re certainly, they’re susceptible to pH degradation and long-term stability they haven’t been used commercially, so I certainly wouldn’t say there’s a gen one and gen two.
I think there’s a series of materials that are available to the practitioner. Which fit in an integrated flow sheet for the brine chemistry that you are working with. I really don’t think one is necessarily better than the other. and again, I kind of, I’ll take you right back, to the start of the conversation, Antoine, it’s like you need a large, consistent feedstock of brine, which guess kind of has to look the same every day of the year.
And you develop the right technology for that brine supply. And that’s the approach that we’ve taken.
Antoine Walter: you’ve developed this right suited technology and this integrated flow chart flow, suit flow process, and that’s your demo plan today, which is running since 2020, if I’m not mistaken.
Andy Robinson: Correct. Yeah.
Antoine Walter: You are setting yourself up for the full scale. What will change between your process today and the one you’ll have in the full scale?
Andy Robinson: the only real change will be that in the full scale plant there will be a recycle stream from the carbonation plant back into the front of the facility. That will probably be about the only major sort of, if you like, integrated flow sheet change relative to what’s running in the plant right now.
Cuz what we’ve got running in the plant basically is, a small commercial facility effectively. It’s just, we don’t sell any of the products that we make, we just run it. On a continuous basis to, to understand the process. But the change from the commercial plant yeah, for the most part it’s just going to be more of the same.
So it’s gonna mostly, we’ve tried to use vendor supplied equipment in the plant. Right now we have tried to invent as little as possible, to be honest, so that we can buy the same equipment just more of it for the commercial facility in the most part. And like I say, one or two recycled loops.
We’ll be integrated
Antoine Walter: What will you be recycling?
Andy Robinson: When you think about any sort of d l e process, you’re spending a lot of equipment. When you’re building the commercial facility, it’s an expensive business. So you are spending equipment to process. All of that flow of water, which comes into the front end of your plant.
And obviously the scale of that flow is dependent upon lithium concentration, but you have to build, you’re in the water business. If you think about the front end of one of these d l e plants, looks a lot like a municipal, water treatment facility. This is large, expensive infrastructure.
These are big pipes, big pumps, big filters, big initial processing equipment which is not cheap. And so therefore there’s a very large incentive to extract as much lithium as possible from your incoming flow. So therefore, when you sort of run through the flow sheet, there are always points where potentially you could lose lithium from the system, which would reduce your overall lithium extraction efficiency.
And you want to keep that as high as possible. One of, if not one of the major in any way, you’re taking a final solution in our case, a mixed lithium sodium chloride solution, and you wish to carbonate it. In any carbonation, crystallization system there is always, what’s called blowdown or there’s always a bleed stream from that crystallizer system, which contains a relatively high proportion of lithium.
So some of that, you can put two other parts in the flow sheet, but there’s typically always needs to be a recycled loop, which we can do really effectively in a DLE project, it’s very difficult to do. For example, if you’re doing your lithium concentration in the Atacama desert and then you’re doing your carbonation crystallization at the coast in Antofagasta for example, Doing that recycle is not terribly efficient because there are hundreds of miles in the way, whereas we can actually recycle on a continuous basis at the most optimal points in our flow sheet.
So we can improve our overall lithium extraction efficiency from start to finish, which is a key metric for us.
Antoine Walter: And how much do you reach?
Andy Robinson: At the d l e stage, we see well over 90% extraction efficiency just in the d l e step. We actually see substantially more in that a lot of the time. And again, that’s not just occasionally, that’s over hundreds, thousands of cycles.
Front to start, we are in the middle of the design phase for the commercial plant right now. So we have a contractor running, what’s called feed front end engineering design study. I think the basis of design, we’re working on a little over. 88 ish, 89% total start to finish extraction efficiency for lithium, which is, huge.
It’s an incredible result, but is supported completely by what we see in the plant. So we’re very comfortable with those sorts of overall efficiencies.
Antoine Walter: I just picked up a muggle question on the way, so excuse me. For really, I assume it’s a MLE question. I’ve been following Elon Musk’s Twitter and I’ve read that lithium producing companies are printing money and you have a demo plant running since 2020 and you’re not selling what you’re producing.
Why? So,
Andy Robinson: Uh,
Because uh, Frank, we are not allowed to at the moment. in Arkansas, and this really does vary from state to state. Within the US and obviously from country to country, but from state to state. The way that the business works that area is that the minerals actually in the ground are owned by the mineral rights owners, which are individuals, families, companies in some cases who own those rights under the ground.
And obviously they are due some money for when someone like us comes along, pumps that resource to the surface and creates value from it. Some portion must go to the people who actually own the minerals, the mineral rights owners. There’s a very well established framework for that, for bromine.
In the state of Arkansas, there is a, an established royalty type structure for other minerals. One for lithium has not been established yet, and it’s in the process of being established. Until that is finalized, we can’t. Sell the product because right now there’s no way that we can then effectively provide the financial feedback to the mineral rights owners.
Antoine Walter: So right now we discussed your extraction process. You have a Brian at the entry, which you run 1, 2, 3 times depending on how it drops out. You get this 88% extraction over the entire process might be even north of 90%, which is really impressive.
Andy Robinson: Yep.
Antoine Walter: That is all set up. You have this feed study done by Koch Engineering.
If I’m right, which is ongoing, which is going for this full scale. And you could be stopping there and you could be producing lithium, and that would be already a significant step forward for that industry worldwide and in North America. But you’re not stopping there. You have pilots ongoing.
You are looking at conversion from lithium chloride to hydroxide. You’re looking at carbon capture. I mean, conversion. I would expect it to be maybe a more conventional pilot, like something which I mean would be rocket science to me, not rocket science to you. Carbon capture sounds like really next step in terms of what you try to achieve there.
So why do you make your life so difficult?
Andy Robinson: Yeah, I mean, great question. And the team might ask me the same question many days of the week as well. So I mean, a couple of different things there. So one, again, sort of take you back to the start of the conversation. One of the reasons why we really like the smackover is its scale.
When I talk about the fee stock coming into the demonstration plant right now, the amazing thing is that when I move 30 miles to the west, to our southwest Arkansas project, or when I move. Another sort of distance over the state line , into Texas to look at those. the feed stop looks basically the same.
The brine composition and quality is effectively the same in all of those locations. The lithium grade improves significantly. So the quality of the resource improves as I move westward. But that means that we have effectively, the development plan that we’re working on and aim to execute over.
Really the next decade is to get the first project built scale and then replicate a across the same resource for the, effectively the same feed stock, and the same technology to process the brain. But the conversion part on the end, that really does differ. Differ because there is definitely a market for both materials whether it’s lithium carbonate or whether it’s lithium hydroxide and certainly.
When we think about the North American automotive market, I’d say, there’s a slightly different psychology maybe than is present for some of the Asian sort of car manufacturers or for the European car manufacturers, where the concept of range and power density is maybe slightly more important in North America than elsewhere.
So you’re seeing certainly amongst the larger automotive OEMs in North America, as there’s a little bit more emphasis maybe on those high nickel cathode materials to produce more energy dense batteries better power generation, et cetera. And those all require a hydroxide product to create those high nickel cathode materials.
So when we think about, the development plans for the company, and we will need to. Have a range of offerings, so carbonate and hydroxide. For sure. The carbon capture one is, that was just one of those sort of slightly serendipitous instances where we were introduced to the technology, which is developed out of Norway.
And it’s a membrane based technology. We use a lot of membranes in our plant. There’s a very high degree of comfort with membrane technology amongst our technical teams. And one thing, whenever you are running a crystallization business, which we will have to use, we’re gonna have to crystallize products, you will always end up burning natural gas somewhere in your flow sheet.
So you will always be generating CO2 emissions from what we are gonna. Build over the next few years. And so the concept of being able to use a novel technology, which offered really kind of interesting and compelling economics, both in terms of capital pricing and operational pricing to capture carbon dioxide out of natural gas burning, flu gas emissions using a membrane technology.
It seemed like a good fit. And yeah, we’ve been fascinated to try it. And we’re also, fascinated with the role of carbon dioxide in everything that we do. So we haven’t actually talked about this, but we’ve been doing some really interesting work using carbon dioxide as a reagent to help with some of the flow sheet work.
So kind of looking to consume CO2 as a reagent in our existing flow sheet. So sort of, beneficial reuse of captured CO2 in the flow sheet. But then also as we kind of scale out across the smackover formation there’s an enormous geological permanent sequestration facility basically.
And, we will be moving more fluid in and out of that formation once we’re at full production than anyone else in the entire region. So the ability to capture co2 use it in our flow sheet and then permanently sequester it where it could be into that geological formation seems like a very compelling story to me and to Robert as well.
that’s the future. that’s the future just embodied in everything that we want to do there. We wanna make responsible lithium chemicals to go into the energy transition story. And if at the same time we can capture CO2 from anything that we do, and then ultimately, Put any additional captured co2, maybe using that aquilo membrane technology back into a permanent geological sequestration reservoir.
Seems like a fantastic story. So it really all fits together from my point of view.
Antoine Walter: I think it absolutely fits together. it’s with this over-delivering, you could be just producing lithium and , that would be fine, but in terms of ESG impact, in terms of. Positive impact all the way through the chain. Especially if you can leverage the CO2 in your process.
It’s like a win, win. Pretty fascinating. And that’s in understatement. You mentioned at the very beginning of this conversation how you want to build a very large company and with the MOV formation, you probably have everything it needs to build that very large company because you have s you have Texas, you have lots of resources, yet let’s assume a crazy French guy comes to you water samples
Andy Robinson: Right.
Antoine Walter: and those happen to be lithium rich.
I have two water samples with me, one at 310 PPM of lithium, the other at 430 PPM of lithium. Of course it’s not just lithium and water. There’s a lot of other stuff inside. Is that something you would. Straightaway wipe off the table cuz crazy people, which come with crazy ideas. You must have that twice a week, if not twice a day.
Or are we speaking here of something which might eventually be interesting to you?
Andy Robinson: Yeah, I mean, I would say that, it would depend clearly if you kinda go back to the start of the conversation, some of those sort of the five things that, that we sort of think about when we think about scale is key. So the size of the formation of the brain resource that’s there is really important.
Those concentrations are absolutely economic. Those are certainly would justify additional investigation. Yeah, for sure. whenever I look at those, if it’s less than 150 PPM lithium, I would always say, that’s gonna be a struggle to ever make the economics truly work Now, future lithium pricing, who knows, right?
So there’s certainly many things there which are to be determined and which could make a lot of marginal projects very attractive potentially in the future. But certainly the, those numbers that you’re talking about there, yeah, that’s a resource which should be looked at some more for sure.
Antoine Walter: Let me try to follow your five step framework. Actually, there’s one of the steps where I don’t have the answer, but for the others I have it. Grades is what I just mentioned. We are above the threshold of 150 you just gave. So, I guess doesn’t speak too bad size. I don’t know. That’s the one I don’t have.
I just know it’s part of a big aquifer and I’m working with geologists to, I mean, I’m still running a podcast and still not a serious project, but I want to do the thought exercise up to the end and geologists have been looking into it, so maybe they can give me the answer on the size at least to have an estimate.
In terms of porous media formation that the underground is very well known and is a porous material, which is documented for decades Centuries. It has been like the region which was transitioning from France to Germany several times over history, and every country has been really mapping the underground.
So that’s known. The permitting is known as well because it used to be potash mining and we would still be producing potash if the Australians would not be able to do it three times cheaper. So, And there is no existing brine processing, but there are water treatments ongoing because there’s also an underground landfill, which burned and which means that they are recycling the water to protect the rest of the aquifer So there is an ongoing water recirculation, not to the scale we are discussing at length as I mean, really far away. So yeah the thing I don’t know is the size from your experience. Aside from answering the question of the size, where shall I start?
Andy Robinson: I mean, uh, the place to start would be to Trial. Some initial, d l e technologies, again at the bench scale and start using some available technologies where you can, there are, a handful of vendors out there right now who have technology and packaged solutions that you could start to try and you could understand initially lithium extraction potential from that brain.
The scale. item is very important. So understanding the extent of the formation, thickness porosity, permeability all of those items are very key. One of the things that I think we’ve been very fortunate from is that the smackover formation, because it’s been exploited for oil and gas for a century and for Brian for six decades, there’s a great deal of numerical modeling experience and reservoir engineering experience within that formation.
And yeah I would strongly recommend that you speak to a reservoir engineer or a hydrogeological modeler who could start to think about Brian Distribution Brian extent. Flow boundaries reservoir boundaries, et cetera, and how that might play into a resource understanding.
one of the things that we have certainly come across is yes, lots of oil and gas companies have come to us over the years and said, Hey, I’ve got this field located just here. And, we’ve got these lithium grades in the field and we’re making all of this produced water, which is a complete pain.
It costs us money can we capture lithium out of it? And there is still an order of magnitude difference between a commercial brine operation for lithium extraction and the volume of produced water, which is co-produced with oil and gas operations. A commercial brine processing business for a mineral extraction where the mineral is only present.
On a few still, in your case three to 400 parts per million, you still have to process a lot of Brian to make a commercial project. So the resource the poor volume has to be large is very difficult to make anything work off a small sort of resource base.
Antoine Walter: Again, I had read that tweet from Ellen Musk. So I was rethinking I was gonna print money in the next month, so I was really happy you just
Andy Robinson: Well, I wish I wish you the very best of luck in printing money from it anjo. I certainly wouldn’t begrudge you that.
Antoine Walter: Just to close , that deep dive. By the way, thanks a lot for everything you’ve shared and the openness in diving into your process and what you’ve been developing, which is truly amazing. If you have a threshold at 150 ppm where you say, starting there, it starts to be interesting.
Does that mean that assuming you get Es and your other our project up to commercial scale. Would you be going into this additional fields or do you really say, we have this competitive edge of understanding this micro of reformation, let’s triple down on it.
Andy Robinson: Yeah, I mean, I think, certainly I would never say never but the immediate focus of what we’re doing. Is the nature of the opportunity and the smack over is huge. So it is a truly world-class resource of a scale, which I don’t think is really matched anywhere else.
Not that I’ve found anyway I could absolutely be proven wrong, but not from the basis of my research over the years I’ve not found anything similar scale, grade, quality anywhere else on, on the planet for lithium. there’s so much ahead of us that as a company and it’s, we grow and we add people and we continue to build out our capabilities in terms of designing, scaling, building, project one, then project 2, 3, 4, 5.
There’s so much ahead of us in the smack over it’s difficult for me to say with a straight face. We should absolutely be chasing other formations right now. But. We will see, like the lithium demand curve is much discussed and structural deficit of lithium chemicals by the end of this decade is certainly seem to be a potential reality.
And who knows what incentives that may generate for a company such as ours to scale more quickly and in other jurisdictions, in other resources. Certainly whilst it’s not in our immediate game plan in a year, two, three years time, who knows Enfor one, this entire industry is just getting going.
It’s been a sleepy little niche business for 40 years, right? And it’s just going through a revolution. And so how this business looks in five, 10 years time, I think it’ll be very different.
Antoine Walter: I just have one more, which I would sneak into it. So really in, in two words, sorry. Is there a race going on to be the first one to be commercially producing lithium with a DD process? Because everybody I met said you are supposed to be the number one, but Vulcan brought some doubt in my mind when I saw that their calendar because it seems like you would be producing at the same time.
Andy Robinson: we certainly hope to be the first new production in North America for lithium from Bryant for sure. We felt comfortable with our timeless cause. again, this is like project development.
Permitting is always on the critical path. For most projects. It’s the bit that doesn’t get talked about. Like on a water podcast. There’s, an emphasis on the water and the technology and the processing. But as a project developer permitting, stakeholder approval, stakeholder buy-in state and local government approval, and the permitting that fits in and around all of that story is at least as important.
One of the amazing things about what we’re doing in South Arkansas is that it’s such a high level of support for what we do. Because we’re effectively building inside the fence of an existing processing facility. Our permitting requirements are minimal because we are using the same infrastructure that’s already in place.
And so there’s just some small permits that you’re relating to our process only, but we’re. There are no impacts. We don’t have to drill any wells. We don’t have to put any pipelines in or any of that. I would say I have a a very good degree of certainty around some of my timelines because I know I don’t need permitting or agencies, or authorities to approve certain things before I can do, then do certain other things.
So I’m comfortable with our timelines, but I mean, I, we need all lithium that we can get, frankly. So I mean, whilst I’d love to win the race as long as we’re soon that’s good enough.
Antoine Walter: Well, Andy I open saying that I had high expectations because you’ve been warmly recommended twice and you over delivered on those expectations. So thanks a lot for that. To round off, I just have very rapid, fair questions, short questions, I mean for short answers. I’ll try not to sidetrack still French, I can’t promise, but I’ll try.
Rapid fire questions:
Antoine Walter: My first profit for a question is, what is the most exciting project you’ve been working on and why?
Andy Robinson: honestly, everything that we do in Sandal, lithium, I mean like building, the plant that we’ve got, we’re even running right now is just still completely exciting. Whenever I go around there and see what we’re doing, it’s amazing. Thinking about building the first one and like. Selling, a ton of lithium carbonate to an end user and it going into a battery and going into an ev that would be amazing.
That would be a fantastic achievement. Be so proud of when we do that. But, I’m very lucky. I have a very interesting job and everything that we do is pretty cool. Even my kids think it’s okay, right? Yeah.
Antoine Walter: Can you name one thing that you’ve learned the hard way?
Andy Robinson: working continuously with natural brain, that’s been like, that’s been a headache. Yeah. That, I, we predicted how lots of things would work, and I would say none of those predictions played out. Everything worked differently than we thought it would do. And so that’s been a really hard lesson.
This stuff is difficult. It seems really simple. Again, goes back to continuous chemical processing. Is. Whilst a lot of it is very simple, the chemistry should be very straightforward. The practical reality is difficult to get right. And so that we’ve learned the hard way. But me personally, I think some members of the team who are who know better than I do and are not quite as optimistic as I am probably new.
But I’ve certainly learned that hard way.
Antoine Walter: Is there something you’re doing today in your job, which you will not be doing in 10 years?
Andy Robinson: I mean, other than using AI to write news releases which I still have to do right now. To keep it, maybe to give it a message for your podcast. I think we spend a lot of time taking discreet samples and sending them internally to a lab for analysis. In the future, I think we’ll see a lot more inline, real time analysis.
Of fluid streams and the control, the process from that inline, realtime analytical tools. So I think that process analytic control through, through real realtime chemical analysis, that will be something that we’ll do in the future that we can’t quite do yet.
Antoine Walter: So here I have to prevent myself very strongly to open a sidetrack cuz I can start another hour if I do. It’s a fascinating field, really fascinating field. So maybe you have to come back at some point.
Andy Robinson: Sure. I’ll bring somebody else on when, who knows a lot more about it, frankly. Yeah.
Antoine Walter: what is the trend to watch out for in the D l E sector?
Andy Robinson: Oh I don’t know if there’s a specific trend to be honest, Antoine, I think it’s the, for people who are truly interested, I think that, again I’ll hark back. It’s people actually telling the full story about their entire flow sheet from start to finish. I think that’s gonna be the interesting, that’s the real interesting thing that investors in the space people who are just have a, a, an intellectual interest in, in, in what we’re doing.
That is the trend to to figure out and understand like what does the whole flow sheet look like and what seems to be working across multiple different formations. From resource to resource. Cuz I think that tells you a lot.
Antoine Walter: Last question, would you have someone to recommend me that? That should definitely invite as soon as possible on that microphone.
Andy Robinson: I mean, if you wish to know about lithium. You should absolutely speak to, to, to Mr. Lithium. To Joe Larry. He would be an excellent podcast guest cuz he knows he’s forgotten more about lithium than most of us know. So that’s just a fantastic person to talk to about how the industry has evolved and where it’s going.
And if you want to know about process analytic control and modern approaches to processing, you should speak to to a friend of mine and a colleague of mine, professor Jason Hein, who is at university of British Columbia, and also Telescope Innovations. He’s a, an individual who we use a lot to lean on as a technical resource.
Probably, actually no, without doubt, the cleverest person I’ve ever met. An incredible individual. So either of those people would be fantastic. Podcast, yes.
Antoine Walter: Thanks a lot for the recommendation I have been exchanging with Joe. I have not been able to pin him down to having on the microphone, but I will keep on trying cuz Yeah, I got the recommendation from others and Robert advised me also to speak to Jaen Hein. So
Andy Robinson: No.
Well, there you go. I didn’t,
Antoine Walter: two recommendations, which is the magical number, which brought you on that microphone.
So it was a good pattern to reproduce. Thanks a lot for the time you spent with me. Sorry I was French and I took more time than expected. If people want to follow up with you, what’s the best place for them to contact you?
Andy Robinson: I mean, really through the standard Lithium website or I can always be emailed at a robinson standard lithium.com. But yeah, and always happy to interact with people who are interested and thank you. I’m fascinating interview and it’s a pleasure to speak with you, Antoine. Truly.
Antoine Walter: again, my pleasure. So thanks a lot and I stand my point. If you want to be back at some point for instance, when your plan starts operating I’d be happy to have you to discuss what you’ve learned in the
Andy Robinson: At that point, We should have a live podcast from the facility. And then we can actually run you through in real time a lithium ion entering the plant, and finishing up in a in a hundred micron particle of lithium carbonate!