Membrane filtration systems are around for a while! Think of the Egyptians, that bettered water quality with ceramic filters, in 2000 BC, or of french physicist Jean-Antoine Nollet that stumbled upon membrane osmosis in the mid-18th century. (And what is a coffee filter, if not a membrane filtration?)
Yet, it’s only since the 1960’s that membranes really took off in the Water Industry. That growth is now really spectacular since the 1990s. Will we soon see membranes in every water or wastewater treatment plant?
This guide will equip you with everything you shall know about the fastest-growing water treatment technology ⬇️
Table of contents
- What is Membrane Filtration?
- How does Membrane Filtration work?
- What are the different families of Membrane Filtration Systems?
- What are Water Treatment Membranes made from?
- What are the different types of Water Treatment Membranes?
- What is Membrane Filtration used for in Water Treatment?
- Advantages and Drawbacks of Membrane Filtration technologies
- What is the Global Market for Water Treatment Membrane Filtration?
- How do you control a membrane treatment system?
- Glossary of Membrane Filtration abbreviations
What is Membrane Filtration?
Water is almost never pure. As the solvent for life, water dissolves a broad range of components, from sand to heavy metals, through viruses, bacteria, or pollens.
Membrane Filtration is hence the act of separating these dissolved elements from water by forcing that water to flow through a membrane.
This classifies membranes as a member of the filtration family, as cousins of sand and activated carbon filters they often compete with, and nephews of coarse filters that are often found in water and wastewater pre-treatment steps.
How does Membrane Filtration work?
As a physical barrier, the membrane acts a little like a sieve, just with much smaller holes to let water flow through.
The pressure difference between the two sides of the membrane – which we call permeate and retentate – generates a flow over it.
Depending on the membrane pore size, it will stop different types of contaminants.
This pore range also influences the pressure needed to induce a flow. Often, a large pore will enable a pressureless treatment, with only gravity as a driver, while advanced treatments featuring the smallest pores involve high pressure and intensive pumping.
What are the different families of Membrane Filtration Systems?
We often classify membranes by the size of the pores I just mentioned. Like the coffee filter I alluded to in the introduction, simple filters we see in our daily lives feature 15-20 micrometer wide pores.
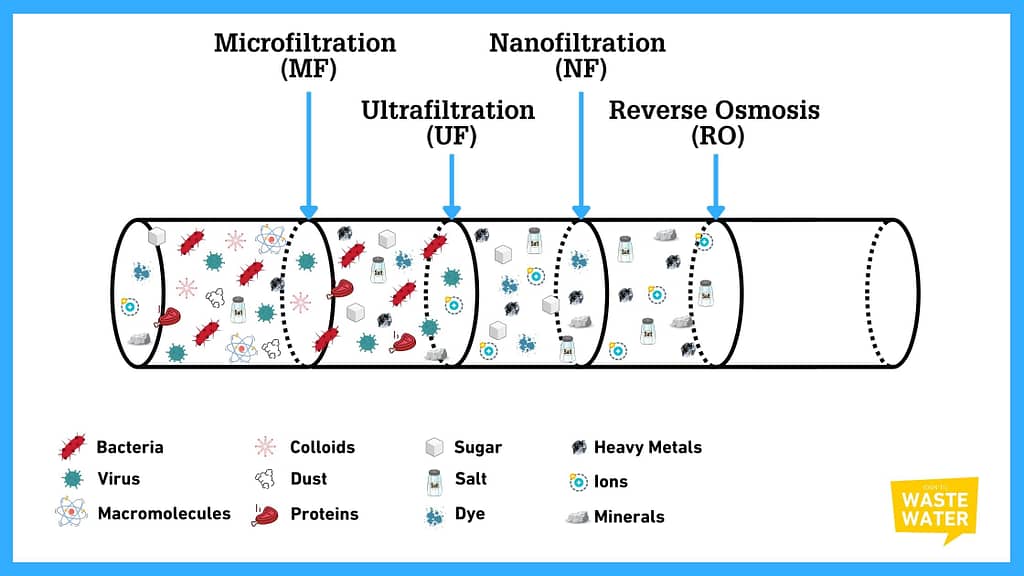
Indeed, we also use paper and towel filters in water and wastewater treatment, yet, we rarely consider those to be membranes. Hence, the membrane range starts with:
Microfiltration (MF)
Microfiltration Membranes feature a pore size ranging from 0.1 to 10 micrometers. Their operating pressure lies between 0.2 and 3 bar.
They would, of course, filter out of the water every larger-sized particle, like sand or any kind of filter medium. But their primary intent is to stop particles, colloids, and bacteria up to a range of 100 nm.
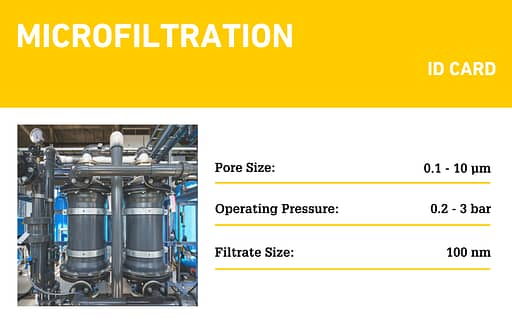
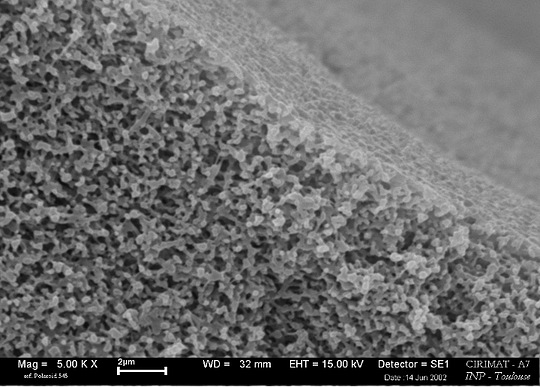
Ultrafiltration (UF)
Ultrafiltration Membranes have pore sizes varying from 0.008 to 0.2 micrometers and operate at pressures running from 0.5 to 10 bars.
You might notice here that there’s an overlap between MF and UF membranes: indeed, there’s no regulation or standard that clearly states that you’re one or the other from a specific pore size on. So, it depends on suppliers’ commercial freedom to qualify their products as ultra- or microfiltration.
I’m breaking down all the types here, but UF and MF are often clustered together as they have similar applications. Exactly like Nanofiltration and Reverse Osmosis, which we will address in a minute, are often taken together.
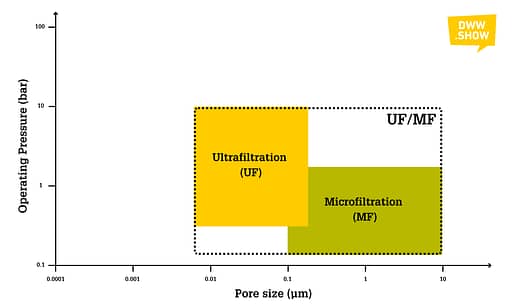
On top of all the components already filtered by microfiltration, ultrafiltration adds a significant additional category of pollutants removed: the Viruses. Hence, from UF on, you can consider membrane treatments of water to be disinfection.
Compared to MF, UF finishes off the Colloid removal, also taking proteins or carbon black out of water.
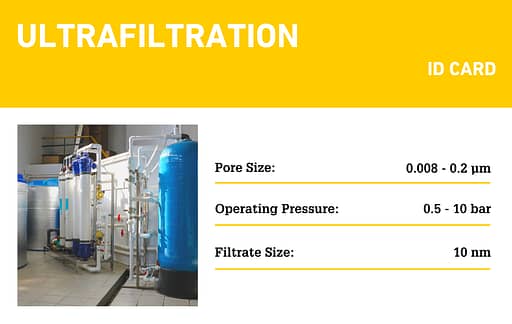
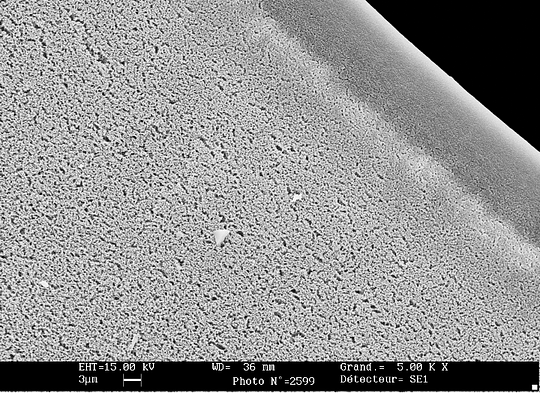
Nanofiltration (NF)
The pore size of nanofiltration membranes runs from 0.0008 to 0.01 micrometers, while NF systems operate between 5 and 20 bars.
Again, there’s an overlap with UF (and on the other end with RO), and it still is a matter of commercial definition.
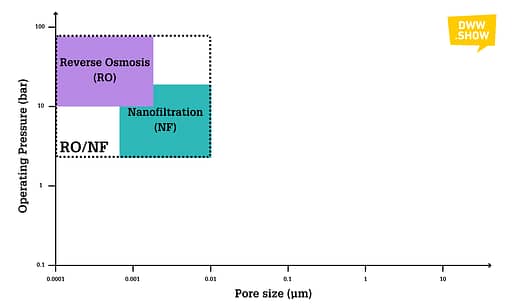
Nanofiltration takes all divalent ions out of water – if you’ve forgotten your high school chemical lessons, those are all the ions featuring two electrons alienation or more, so the likes of Sulphide (S2-), Chromate (CrO42-) or Calcium (Ca2+). In less chemical terms, it also means removing sugars, dyes, and a vast majority of pesticides.
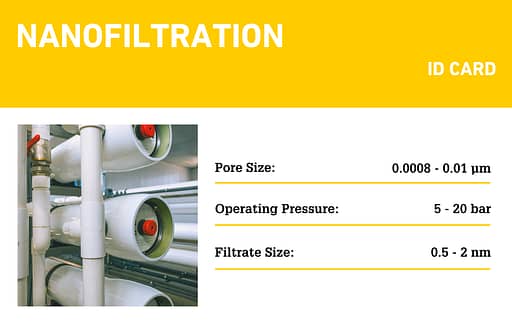
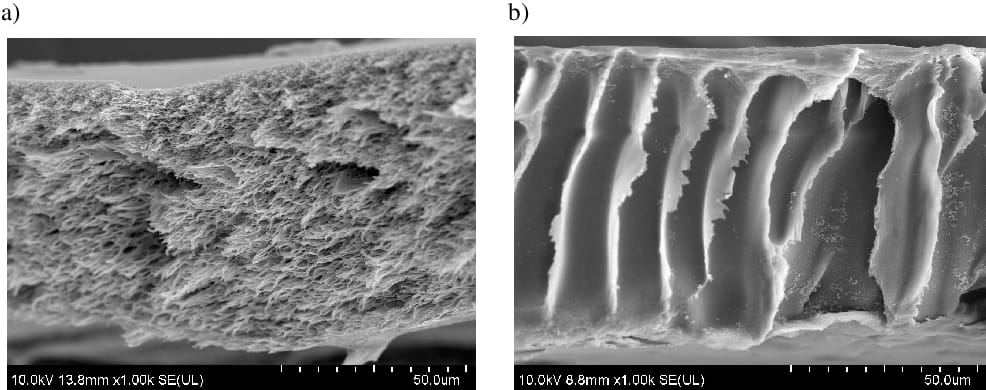
Reverse Osmosis (RO)
Some people still sometimes call Reverse Osmosis “Hyperfiltration.” Even if this is very rare, it hints directly at what it is: membranes with pore sizes ranging from 0.0001 to 0.004 micrometers, with operating pressures between 10 and 80 bars.
This last stage in the membrane pyramid would take out any remaining ion, for instance, heavy metals. But the most iconic use of RO is its ability to remove dissolved salts from the water!
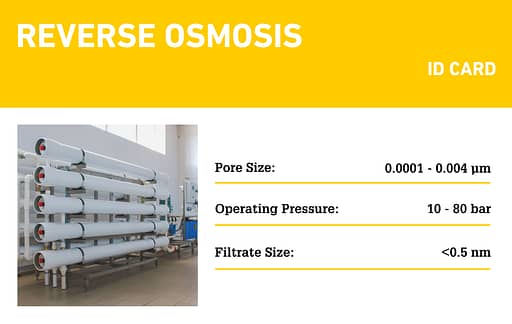
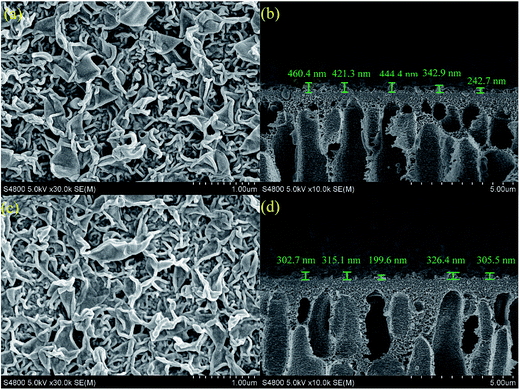
Forward Osmosis (FO)
It is probably worth mentioning here that when you reach membranes with particle size in the range of Reverse Osmosis, those become only semi-permeable. Indeed, pore sizes become very close to the atomic radius, which means that even water has its struggles to flow through!
As a result, both reverse and forward osmosis leverage the natural mechanism discovered by Jean-Antoine Nollet in 1748. This means that the solvent only moves from one side to the other of the membrane when water is present on both sides.
To activate this mechanism, Reverse Osmosis would apply pressure to go against the natural flow, while Forward Osmosis really goes with nature. Now, even if it represents a sexy technological evolution with less pressure required, Forward Osmosis still struggles to be deployed on a large scale.
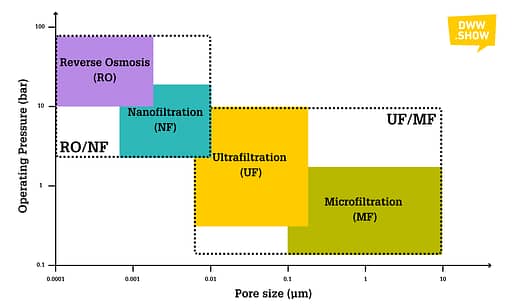
What are Water Treatment Membranes made from?
Beyond the pore range, which we just explored in-depth, there are two more key characteristics to define our membranes. First, what material they’re made of, and then what shape they have.
Let’s start with the materials:
Polymeric Membranes
These are by far the most common type: polymeric membranes represent 93% of the MF/UF market and almost the entire NF/RO one.
We can further split polymeric membranes down into two categories: hydrophilic polymers (cellulose acetate, chitosan, PVA…) and hydrophobic ones (PVDF, PP, PES…)
Hydrophilic Polymers
Hydrophilic polymers were long market leaders, as their core characteristics enabled higher flow rates and lower operating pressures.
As membranes have the tendency to clog – aka, to get their pores blocked by pollutants, hydrophilic materials are interesting to restrict that phenomenon. Indeed, you can fully regenerate them through deep backwashing, which avoids irreversible clogging and gives a theoretically better operating cost over time.
Now, that is also widely theoretical, in the sense that these materials (e.g., cellulose acetate) have limited resistance to chemicals, don’t accept pH below 3 or above 8.5, can be degraded by bacteria, only work up to 35°C and are weak to hydrolysis and oxidation.
So yes, they might better resist clogging, but you would still need to replace them regularly as almost everything else destroys them in the long run.
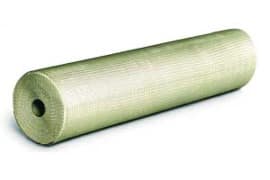
Hydrophobic Polymers
Those almost fully took over the previous category nowadays. In the 90s, they were slightly more expensive, but that’s no longer true today, even if oil price fluctuations, of course, affect them, as hydrophobic polymers are almost all made of plastics.
Materials like PVDF, PP, or PVC resist to temperatures up to 75°C, pH all above the range from 1 to 13, and also very well survive chlorine and micro-organisms. We’ve already seen their drawback: they are subject to irreversible clogging, which means that even deep back washes won’t restore their factory capabilities.
An emerging trend tends to coat those materials to limit their hydrophobic characteristic and build upon the advantages of both worlds.
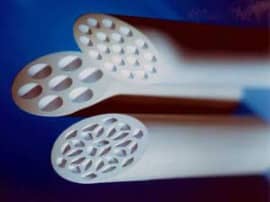
Ceramic Membranes
Doing the quick maths brings us to the naked truth: today, ceramics only represent 7% of the MF/UF market and are in very early steps of penetrating the NF/RO stage.
The historical reason is linked to costs. Ceramics were always more expensive than polymeric membranes. And hence, while polymerics rapidly benefitted from scale effects with the rapid expansion of membrane treatments, ceramics were left behind.
Now, since the beginning of the 21st century, the costs of polymeric membranes almost follow a “Moore’s Law” curve. It was divided by ten every decade! That decrease will reach an asymptote, but it seriously brings ceramics into the game.
Indeed, as a filtration material, ceramic membranes were always deemed to be better than their polymeric counterparts. They allow higher flux rates. They don’t require chemicals for backwashing. Their higher mechanical resistance enables better lifetimes. And you can coat them similarly to hydrophobic polymers to enable advanced treatments such as PFAS removal.
Today, there’s a last frontier with the RO/FO pore size that’s hard to produce consistently in ceramic furnaces. But UF and NF were already said to be impossible! The industry found a way, so I wouldn’t be too surprised to see Ceramic RO Membranes in the future.
Other types of Membranes
Other types of inorganic materials lend themselves to the production of membranes. For instance, the oil and gas industry features stainless steel membranes with very small porosities in gas separation.
But this has always been too expensive for water applications while not bringing any significant process added value. Further ultra-niche materials exist, yet not by any scale relevant to this guide.
What are the different types of Water Treatment Membranes?
So, we’ve seen pore size and materials. There’s one last characteristic left: the shape of our membrane. But before exploring that one, it’s maybe important to factor in some context.
Indeed, pore range was a purely objective definition. There might be some overlaps from one range to another, but there’s a direct correlation between the width of the pollution you intend to remove and the pore size of your membrane. You won’t be able to desalinate water with microfiltration. And removing colloids with reverse osmosis would be major overkill.
The material characteristic is already slightly more subjective. Whenever you discuss the total cost of ownership as a decisive criterion, you have to make lifetime assumptions. For instance, yes, ceramics sound more robust than polymerics, but no one has ever operated a ceramic filtration plant for 40 years either, as the technology is still too recent.
But that subjectivity is still nothing compared with the debates around membrane shape. Each membrane manufacturer has a sound explanation as to why the type he builds is the best. And the best experts have been struggling for years to determine anyone to be right or wrong.
So I’ll try to be objective, and I apologize beforehand if I go against someone’s convictions!
Hollow Fiber Membranes
Hollow Fiber Membranes have water crossing their envelope to flow, whether from their center to the outside (in-out) or from the outside to their center (out-in).
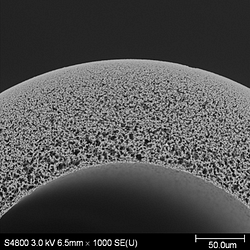
In water treatment processes, hollow fiber membranes are brought together in cartridges or filtration modules. Whereas in wastewater processes, they can float freely between two racks.
These membranes are said to have a strong mechanical resistance and a limited footprint, as they have limited dead volumes. Their conception makes it easy to backwash yet is a limiting factor in the case of high viscosities.
Finally, there’s almost a “religion in the religion,” as you’ll find arguments to explain why out-in is superior to in-out (and the other way round). And finally, people advocating for crossflow.
But who am I to say which one is the best process?
Tubular Membranes
Tubular membranes resemble the hollow fiber ones in crossflow configuration and sealed modules. Indeed, we place our membranes inside a porous tube, and the tube then goes into a cylindrical shell to form that said unit module.
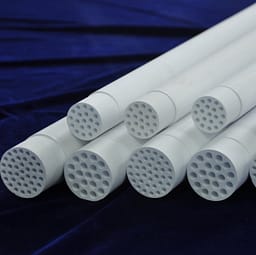
This process offers better handling of high viscosity or high solid content fluids and is the easiest of all to clean.
Now, as it offers a limited specific surface-to-footprint ratio, it requires many more modules than a flat sheet or hollow fiber. It is also quite bulky and, accordingly, rather expensive.
Flat Sheet Membranes
Sometimes called “Plate and Frame” membranes, these membranes are built around a series of flat sheet membranes and support plates.
The water to be treated passes between the membranes of two adjacent membrane assemblies. Finally, the plate supports the membranes and provides a channel for the permeate to flow out of the unit module.
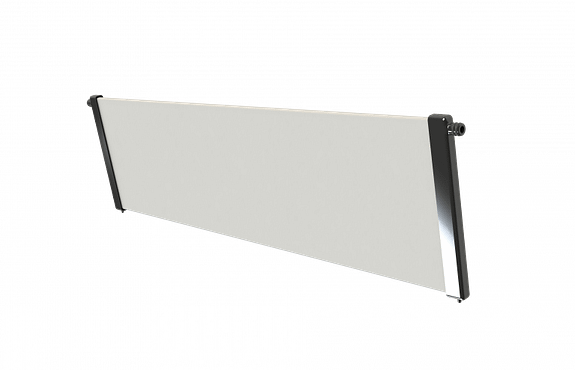
This design enables very straightforward modularity and shares with the hollow fiber one of the characteristics of allowing low footprints and optimizing the hydraulic design.
On the drawbacks side, it is said to be subject to clogging and harder to backwash.
Spiral wound Membranes
This time, imagine a flat sheet membrane that we would wrap around an axis instead of installing it flat.
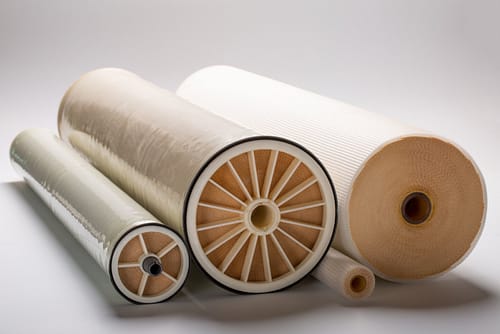
We often see this configuration in processes like MABRs (Membrane Aerated Biofilm Reactors) and it offers interesting characteristics. Indeed, the specific surface to footprint ratio is the highest, limiting costs and installation space.
Now, on the other hand, when you’re applying it in a process where clogging and fouling is not an advantage but rather a problem (so, outside MABRs), this design makes it difficult to control.
What is Membrane Filtration used for in Water Treatment?
Let’s start with a bit of history!
The initial quest in the early 1960s was the search for a way to desalinate water – something we’ve covered in my list of the five most influential people in the Water Industry.
And indeed, that’s the first area that was successful, as thermal desalination really wasn’t much of a good solution. Then, for 30 years, membranes struggled to make a dent in any other vertical or process of the water industry. If you recall what Graeme Pearce shared, membrane companies were rather laughed at as proponents of a technology that would never succeed!
Yet, a revolution was around the corner, with the growing concern around cryptosporidium in the 1990s. About four microns in diameter, this parasite was indeed small enough to get through conventional treatment. As membranes were a complete barrier, the regulation enforced them in 5-10% of all drinking water plants in the UK and US.
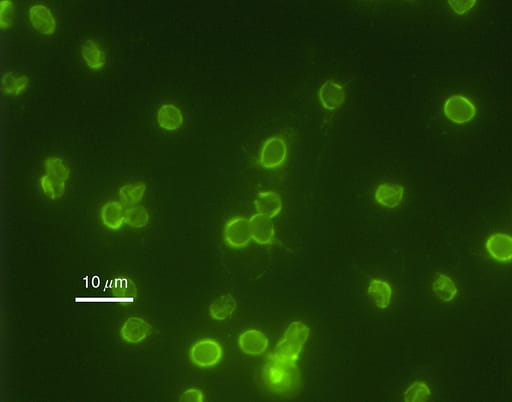
At the same time, continental Europe was trying to reduce its chlorine usage and hence saw in the membrane’s ability to sort viruses and micro-organisms a good way around chlorine’s use – and carcinogenic by-products.
This, in turn, brought a spectacular scale effect in the membrane industry, resulting in tumbling prices that made membrane cost-competitive in almost every process and application.
Where do Membrane Systems fit into a Water Treatment train?
RO and NF membranes have quite a wide range of applications:
- 45% of these systems are used in seawater and brackish water desalination
- 20% go to drinking water production
- 25% serve in ultrapure water generation
- The remaining 10% are used in wastewater treatment, to power reuse applications
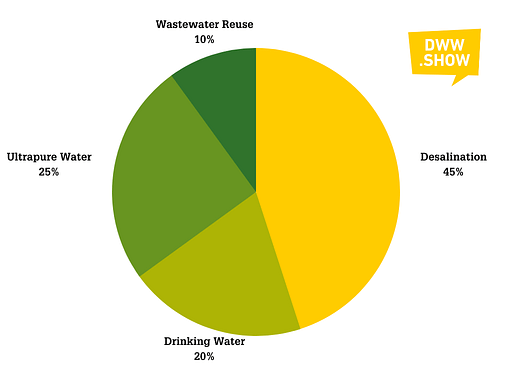
The picture is slightly different for MF and UF:
- 80% of the membranes are used in wastewater treatment. Widely as the workhorse of membrane bio-reactors, then also as pre-treatment for reuse processes
- 11% are the “historic” application in drinking water as a way to replace and enhance sand filters (especially in karstic regions) and sort out viruses and other cryptosporidia
- The remaining 9% are featured as pre-treatment for further RO/NF membrane systems in desalination and ultrapure water treatment
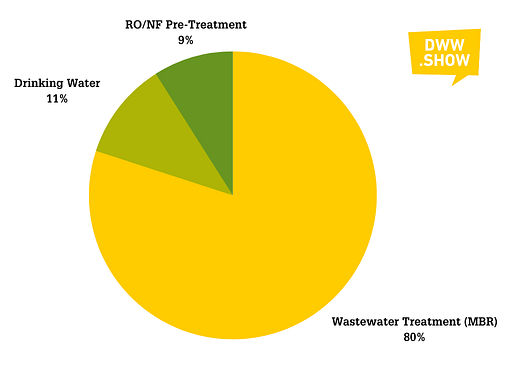
Advantages and Drawbacks of Membrane Filtration technologies
If membrane systems took off over the past 30 years, it’s not only because they became cost-competitive. It’s also thanks to solid advantages. Now, to my knowledge, silver bullets still don’t exist in the water industry, so we’ll see that it also comes with some drawbacks.
What are the advantages of Membrane Treatments?
I would see 6 main advantages of membrane treatments:
1. Membrane systems offer high performances
… and that comes with a welcome side-effect: those are very stable in time.
For instance, to reduce turbidity in drinking water production, you can use sand filters, and they will be effective most of the time. But if you encounter some raw water peaks, those peaks will also be there by the outlet, and your water will not be potable. On the other hand, an ultrafiltration system will always remove these suspended solids, regardless of their concentration by the inlet.
2. Membrane processes are very compact and modular.
So you can fit them in almost every configuration, rack them, put them in layers… And if treatment loads vary over time, you can easily add or remove treatment capacities. Or at least in an easier fashion than with bulky and large technological alternatives.
3. Membranes are very versatile.
You can design your plant for certain pollution and end up treating another, as long as those have similar sizes.
4. You can run your process chemical-free.
At least for everything that touches your produced water (backwashes still often feature chemicals). So, you have an alternative to the potential drawbacks of oxidative disinfections.
5. Membrane-driven solutions are effective from a small-scale on
This makes them a very convenient solution for small plants, especially in distributed and decentralized processes.
6. Simple operation and automation.
A membrane process is driven by a limited number of simple parameters (more to that in a minute). This means that if designed and commissioned right, it can be pretty simple to operate. This also opens interesting avenues for remote control and is again an asset in the distributed or decentralized scenario.
What are the drawbacks of Membrane Systems?
This time, my list features three drawbacks:
1. Membrane fouling.
We’ve seen how various materials and designs exist in the world of solutions. And the dominant ones today share this drawback of relative weakness in fouling. This, in turn, commands a thoughtful design of the cleaning process and a regular replacement of modules or plant upgrades. Now, every challenge comes with an opportunity, right? If you can control the irreversible clogging through biofouling, you can also optimize your plant’s lifetime. That’s another opportunity for the right sensors, with the right brain associated in the right place.
2. Concentrated pollution.
Membrane systems work the same in all sizes: they produce two streams. The first one is clean as per your design. But the second one is just the same pollution you had at the inlet, concentrated in much less water. That’s what we call brines, for instance, in desalination. And, that’s a pollution you have to take care of, somewhere in your process!
3. Limited lifetime.
Due to the fouling and the physical constraints membrane systems have to withstand, they don’t last as long as your good old concrete tanks filled with sand. Depending on how you operate a polymeric membrane system, you’ll have to replace the membrane modules every 7-15 years (less often if you’re using ceramic membranes).
What is the Global Market for Water Treatment Membrane Filtration?
If we look only at the modules, the global membrane market represented $3.2 billion in 2021 (with a half-half share for the MF/UF block on one side and the NF/RO on the other one).
When we factor in the membrane systems (e.g., skids, peripherals, headers), we reach an $8.8 billion market (this time, MF/UF represents 60% and RO/NF 40%)
What trends drive the future of membrane systems?
Christopher Gasson recently told me that “most intelligent people, know, that’s impossible to say what the future’s going to be.”
So call me stupid or laugh at me in ten years; I’m nevertheless going to try with these five trends:
- Membrane Desalination will keep booming and recover its 2007 growth levels. If the World really misses 40% of the water it needs to strive in 2030, it will require its installed desalination capacity to double in a decade (not accounting for further uses of water, such as the production of green hydrogen)
- Water Reuse will develop for the exact same reasons. And there, we’re talking of tripling our installed treatment capacity – all of which will require MF/UF Membranes for pre-treatment and indirect reuse, NF/RO Membranes if we go for direct potable reuse or industrial applications
- Further expansion of the Membrane Bioreactor (MBR) growth. Today, China installs 65% of the World’s MBRs. Stringent environmental regulations are pushing this, together with reinforced incentives to close the water loop. Regulations are here to stay, and MBRs offer a unique synthesis of high-end treatments, low footprint, and efficiency at many scales.
- Emerging contaminants. Those may be PFAS, micropollutants, heavy metals, microplastics, or endocrine disruptors: one thing’s for sure, they will not leave the water cycle on their own. So, if we want to chase them down, we will need advanced treatments, such as coated membrane technologies. When will regulations push for that? It’s only a matter of time.
- Polymeric membrane market’s disruption through ceramics. This is probably the riskiest bet on this list. But if ceramic membranes keep becoming cheaper and are reinforced as technically superior to polymerics, why would we still use those in, say, a decade?
Who are the main players in the membrane filtration industry?
Here’s a list of the main companies that are active in water treatment membrane filtration:
- SUEZ WTS / now part of Veolia – active both on drinking water and wastewater sides of the business, where it features the historic player with the ZeeWeed/ZeeLung product line
- Asahi – quite active in UF/MF polymeric membranes. The company also owns some Forward Osmosis patents that it could activate in the future
- Dupont – active on all ends of the industry, with OxyMem (a leader in MABRs), Memcor (low-pressure membranes), Filmtec (spiral wound), and Inge (MF/UF modules)
- Koch – featuring low-pressure membranes, MBR solutions but also RO/NF systems
- Kubota – a potent player in MBRs, especially on a small scale, also active in flat sheet UF membranes
- Mitsubishi – there’s hardly a portion of the industrial World where Mitsubishi doesn’t have stakes, right? Well in membranes, they produce MBRs and membrane modules for the high-end applications
- Pentair – World famous for the X-Flow membranes it acquired from Norit. Also a provider of peripherals through Codeline, and a market leader in PES membranes overall
- Toray – Quite a differentiated approach here, with PA membranes all over the pore width range while also featuring a PVDF range. Sometimes they also act as an EPC through Suido Kiko Kaisha.
- Hydranautics – One of the membrane pioneers, that later specialized in NF/RO systems
- LG Chem – a mighty RO membrane supplier since they acquired NanoH2O in 2014
- Toyobo – A strongly differentiated RO membrane player, with its hollow fiber solution
How do you control a membrane treatment system?
You can control a membrane treatment skid with simple, sturdy parameters.
From regular filtration to backwash through a membrane health check and deep cleaning, there’s no need for high complexity! This is, again, what makes membrane treatments so well suited to decentralized applications. Indeed: with a handful of sensors and actuated valves, you can already run a UF skid.
For instance and just to name three, a significant pressure drop between inlet and outlet indicates the need for a backwash. A turbidity measurement tells how much water needs to be filtered, and at what speed. And an increased conductivity signals that some membranes might be broken.
Is this a field you’d like me to dive deeper into? Come tell me in the comments, or reach out to me directly, I’d be happy to help!
Glossary of Membrane Filtration abbreviations
Oh gosh, did I use crazy expressions and acronyms? Let’s make these clear here.
- MBR – Membrane Bioreactor
- MABR – Membrane Aerated Biofilm Reactor
- TSS – Total Suspended Solids
- AMTA – American Membrane Treatment Association
- DPR – Direct Potable Reuse
- IPR – Indirect Potable Reuse
- Brines – The concentrated saltwater that results from a desalination process
- CIP – Cleaning In Place (or advanced backwash)